How-to & Style
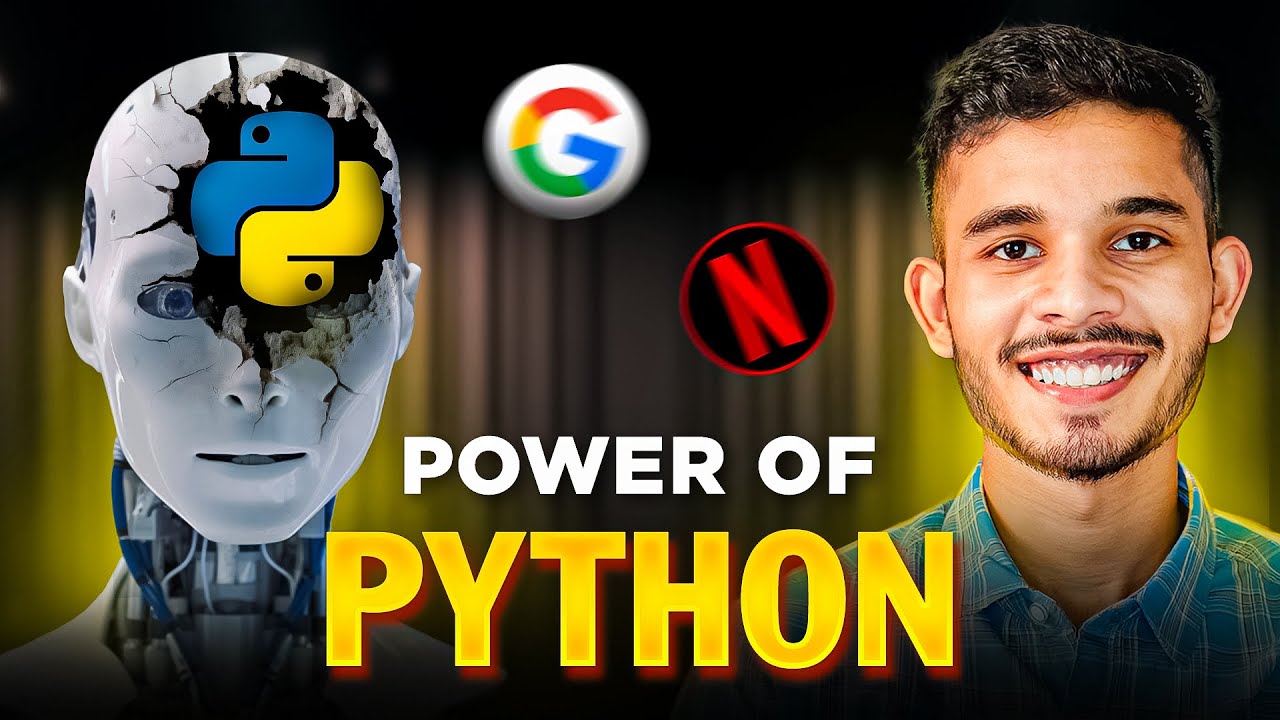
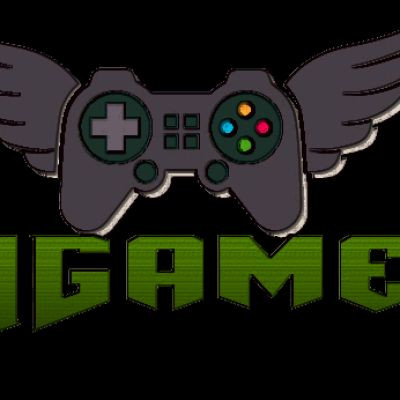
Apply for LIVE Python Placement Program (AI Oriented) Batch - https://codingwise.in/python-e....ngineering-launchpad
Get 700+ Ready-made Projects Code👇
https://codingwithsagar.in/project-bundle/
Discover the power of Python for AI, machine learning, data science, and web development. This video covers practical uses and essential techniques to help you master Python programming.
👋 Topics Covered:
Python for AI: Key libraries and applications.
Machine Learning with Python: Building predictive models.
Data Science with Python: Data analysis and visualization.
Python for Web Development: Creating dynamic web apps.
🤔 Why Python?
Python is easy to learn, versatile, and widely used in tech. It’s the preferred language for AI, ML, data science, and web development.
Key Points:
Step-by-step coding tutorials.
Best Python libraries and frameworks.
Tips to improve your Python skills.
🔥Project Playlist🔥
🔑 Access the Python Programming for Beginner Series
1- Introduction to Python - https://youtu.be/H2qXCexJxgw?si=O1EqZz9iofYL7Mtu
2- Comments in Python - https://youtu.be/VcPe_xY5gMk?si=_xewX8KPAIlGc1Bk
3- Print( ) in Python - https://youtu.be/31i60-8ZJVo?si=otW5BAWZzs5WRbEw
4- Variables in Python - https://youtu.be/jVBXaZ0H0zo?si=jcveRAIg81315bS1
5- Data-types in Python - https://youtu.be/DOm_dlmw820?si=1aU6RttzxRoH-CtW
6- String, List & Tuple In Python - https://youtu.be/MQ6lEUEHIkc?si=fspawVqBbcfPwLsp
7- Dictionary In Python - https://youtu.be/Wd9-OkzSeao?si=oGUisgW0paXmuDEq
8- Input function in Python - https://youtu.be/onLBUIYv6lI?si=Nk9UOVQ7VHdNrtZz
9- String Manipulation In Python - https://youtu.be/kMRliZK2BU4?si=WLOIX36WMCbkZ2pK
10 - Operators In Python Part-1 - https://youtu.be/Vqk1AjKDjzs
11- Operators In Python Part-2 https://youtu.be/jZ1IhJMosJ8?si=quGF7QWE3_PVFogw
12- Conditional Statements In Python - https://youtu.be/xSTh3mcnKGE?si=P3IeN8u4vSyY9i6k
13- Loops In Python - https://youtu.be/to_s1R14RNQ
14- for loop in python - https://youtu.be/X5_cTYg-zbI
15- nested loop in python - https://youtu.be/JzOtBOF5dWc?si=bZcr_NogZ7hqY4xL
16- Functions in Python - https://www.youtube.com/watch?v=eTt8Kiyc8PM
17- String in python - https://youtu.be/EzrwucjQhWA
18- Lists In Python - https://youtu.be/fUJ4iVg6W_8
🔑 Access the Python Project for Beginner Series:
1- Image Slideshow Project - https://youtu.be/nJQpc0IE1GY?si=kwYVnfBLcWp1n7oc
2- QR Code Generator to Accept Payment - https://youtu.be/XR0qVaNNaAo?si=Ke0M5zYwTAWfZFKd
3- Text Editor App - https://youtu.be/mCBTrr_R4qw?si=zgSvfO6OTNRI8AYA
4- Automate your Task - https://youtu.be/V6NdO56x7CY?si=QwkZ2DKLj6x5CWTc
5- Create a Digital Clock - https://youtu.be/kDkN3WPESoY?si=ua--399cNtkif3Vs
6- Tic-Tac-Toe Game - https://youtu.be/Dx7pQV0ZTso?si=HJ50WxVAsV5uHIax
7- Rock Paper Scissor - https://youtu.be/OvsoAMA_P00?si=6cSX-rpWHYdlFGiB
8- Rent Calculator App - https://youtu.be/iCwkuJOxvRI?si=JHnsOOIasWLTS3US
9- Student Management System - https://youtu.be/6e8IqXVZUBk
Connect with us:
Instagram - https://www.instagram.com/codingwithsagar
Telegram - https://telegram.me/sagar4840
Youtube - https://www.youtube.com/@codingwithsagarcw/
Keywords:
Python programming
Python for AI
Python for machine learning
Python for data science
Python web development
AI with Python
Machine learning with Python
Data analysis with Python
Python coding tutorials
Python projects
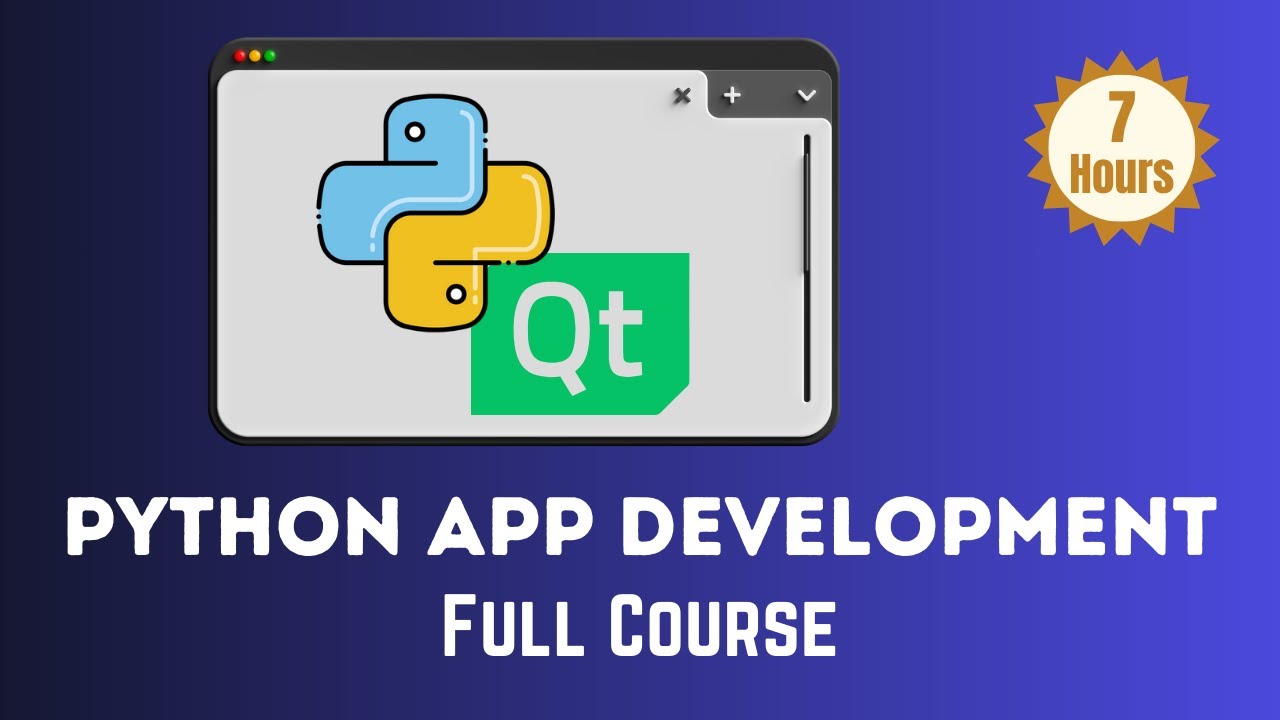
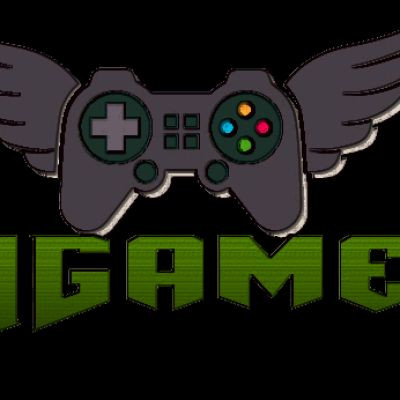
Get my Python & Git Guide, FREE ~ https://thenerdnook.substack.com
Get my FREE Python courses: https://zerotoknowing.gumroad.com
For a better viewing experience and access to all my learning resources as well as tons of other free benefits, please go to my course website!
Full Course:
https://zerotoknowing.gumroad.com
🔔 Subscribe for content that helps you grow!
MY COURSES ON UDEMY:
👨💻 Python Crash Course for Beginners: https://www.udemy.com/course/z....ero-to-knowing-pytho
💻 App Development Crash Course: https://www.udemy.com/course/b....uilding-apps-with-py
🛠 Object Oriented Programming Crash Course: https://www.udemy.com/course/z....ero-to-knowing-objec
🔗 LINKS:
- Get my Python & Git Guide, FREE ~ https://thenerdnook.substack.com
- Check out my Free Python Courses: https://www.zerotoknowing.com
- My Premium Newsletter Free Trial: https://tinyurl.com/4jp3kn32
- Get Early Access to all My Content - https://tinyurl.com/7rnnkp8c
- Stay Safe Online with my VPN deal: https://go.nordvpn.net/aff_c?offer_id=15&aff_id=101468&url_id=902
- Keep all your Passwords Safe: https://go.nordpass.io/aff_c?offer_id=488&aff_id=101468&url_id=9356
- 15% OFF All Merch (Use EARLYBIRD) - https://tinyurl.com/yeyuzdyd
(These support me at NO extra cost to you, Thanks!)
---------------------------------------------------------------------------------------------------------------------
In this comprehensive tutorial, you'll embark on a journey to create sleek and modern graphical user interfaces (GUIs) using Python and PyQt, perfect for desktop app development.
Throughout this 7-hour course, you'll dive deep into the fundamentals of Python GUI development, learning essential techniques to build powerful desktop applications.
Whether you're a programming novice or looking to expand your skills, this course is designed to guide you through every step of the process.
You'll gain valuable insights into Python GUI development with interactive real world projects.
💌 Free Weekly Python Insights: https://thenerdnook.substack.com
☕️ Say Thank You, Buy me a Coffee ~ https://www.buymeacoffee.com/codewithjosh
List of Apps You Will Build:
1. Starter App
2. Calculator
3. Image Editor
4. Expense Tracker
5. Interest Rate Finder
Tools You Will Use:
- Python
- PyQt
- SQL
- MatplotLib
- Pillow (PIL)
- Lambda
Plus, PyQt's seamless integration with Python makes it the ideal choice for developers of all levels.
Don't miss out on this opportunity to take your Python skills to the next level and become proficient in building modern GUIs for desktop apps.
🎯 Subscribe ~ https://www.youtube.com/@codew....ithjoshoffical?sub_c
MY OTHER SOCIALS
🎙 My Podcast - PyPod Chronicles - https://thenerdnook.substack.com/podcast
🌏 My Website - https://www.zerotoknowing.com
📝 My Blog - https://thenerdnook.substack.com
✈️ Life is a B*tch - https://lifesabitch.substack.com
👨💻 LinkedIn - https://www.linkedin.com/in/josh-wenner/
💻 GitHub - https://github.com/Joshwen7947
🔹🔹🔹🔹🔹🔹🔹🔹🔹
CHAPTERS:
0:00 - Introducing Code with Josh’s Free GUI Course
2:20 - Our GUI Course Structure
7:22 - Installation Python and VS Code Extensions
10:30 - What is PyQt?
15:46 - The Basics of a Windowed Application
36:55 - Create a Starter App Window
42:07 - Learn to Design with BoxLayout
50:45 - Add Widgets to an Application
57:30 - App Functionality with Signals and Slots
01:02:52 - Build a Calculator App with Python
01:48:14 - Styling with CSS in Python
01:54:09 - Building an Image Editor Application
02:09:45 - Introduction to Pillow (PIL) in Python
02:28:24 - Implement Pillow with PyQt and os module
03:13:30 - Learn to Use Lambda Functions in Python
03:42:53 - Build a SQL Expense Tracker
04:01:41 - Introduction to SQL with Python
05:16:58 - Build an Interest Rate Calculator with Matplotlib
05:50:33 - Introduction to Data Visualization with Matplotlib
06:28:10 - Toggle a Dark Mode
06:40:15 - Graduation of our course
#python #pythoncourse #coding #pythontutorial #course #learnpython #pyqt5 #pyqt #appdevelopment #PythonAppDevelopment #BuildModernGUIs #programmingtutorial #techeducation #codingforbeginners #softwaredevelopment #pythonprogramming #GUIProgramming #PyQtTutorial #learnprogramming #techskills #onlinelearning #pythonforbeginners
Build Modern GUIs, Beginner's Course, Python GUI, PyQt, Desktop App Development, Python Programming, GUI Programming, Python GUI Development, Python GUI Tutorial, Python Desktop Apps, GUI Design, Python Projects, Programming Tutorial, Python Development, Python Beginners, GUI Development, Python Learning, Learn Python, Python Course, Python Tutorial, Python Programming Language, GUI Applications, Python Skills, PyQt Tutorial, Desktop Application Development, Python Coding, GUI Programming Tutorial, Python Software Development, Python GUI Projects
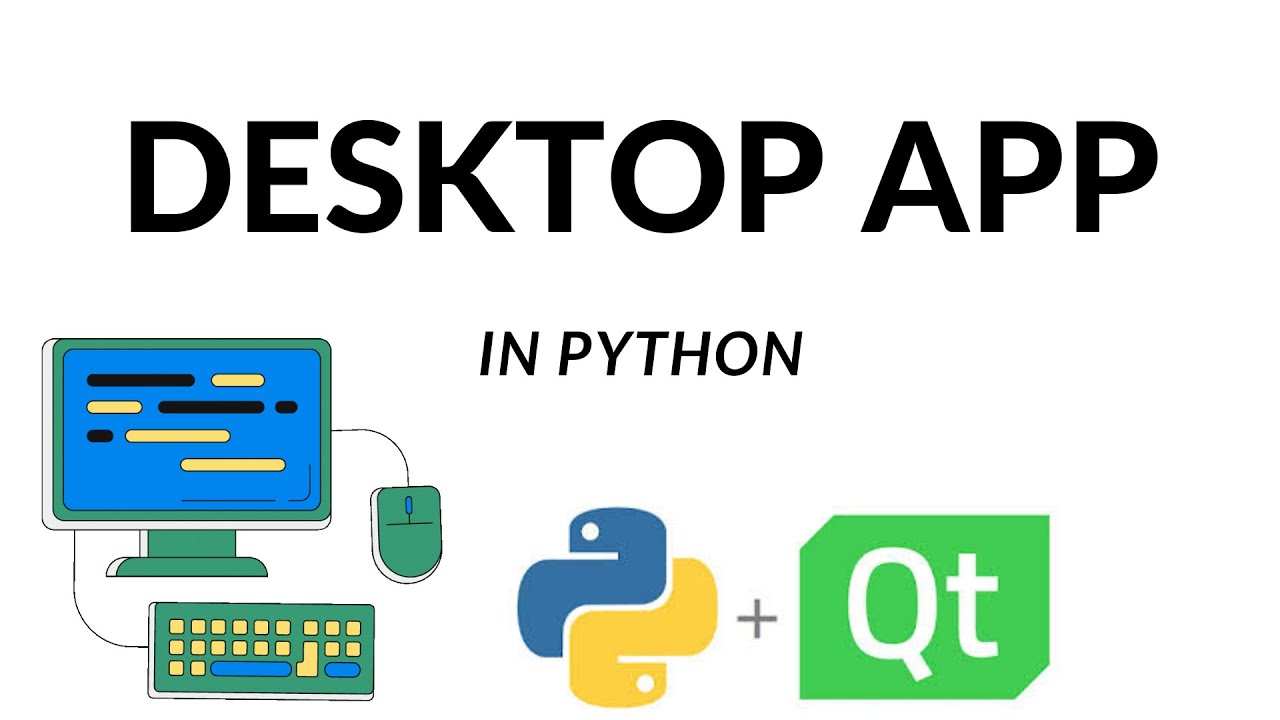
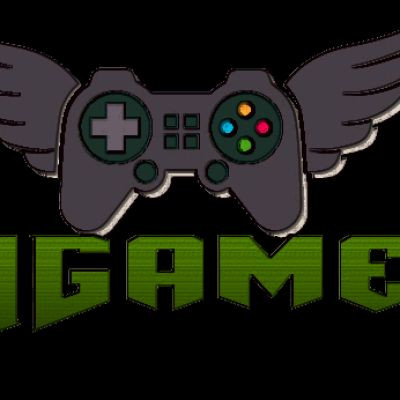
Let's create a desktop application in Python together!
Python source codes : https://l24.im/7BMlCV
In this tutorial, I taught the basics of desktop application development in Python. We determined the dimensions and starting position of a desktop application we created. We've added a photo to our desktop app. In the next videos of the playlist, I'll teach you the basics of desktop app development in Python step-by-step.
I am making a playlist where we will develop desktop applications using Pyqt5 in Python. If you are tired of seeing a black console while learning programming languages, you can develop desktop applications in Python by watching the videos in the playlist in order.
You can see new videos and posts by following our social media accounts!
Youtube Channel ➤ https://l24.im/DzYhx
Instagram ➤ https://l24.im/exaPM
Twitter ➤ https://l24.im/ryzbQ9
Contact address ➤ tescenterinfo@gmail.com
Download QT Designer ➤ https://l24.im/mFKLQUX
Download Python ➤ https://l24.im/W9jEg2e
Download PyCharm ➤ https://l24.im/YHZXc
-----------------------------------------------------------------------------------------------------------------------------------
Video Series:
Python Pyqt5 Tutorial ➤ https://l24.im/jPVh
PYTHON TURTLE TUTORIAL ➤ https://l24.im/b4T3A7d
PYTHON GAME TUTORIAL ➤ https://l24.im/MJ7h
Other videos:
How to make a Twitter Bot in Python? ➤ https://l24.im/u2
Simple Flappy Bird Game in PYTHON ➤ https://l24.im/Eet2
Web automation in python for beginners ➤ https://l24.im/OjqNlf
Instagram automation in python ➤ https://l24.im/aAjiW
Snake Game in PYTHON ➤ https://l24.im/oWrJQs
TIC-TAC-TOE Game in PYTHON ➤ https://l24.im/ceNI
Fidget Game in PYTHON ➤ https://l24.im/pugEqir
Shape Game in PYTHON ➤ https://l24.im/w6MUL
Flappy Bird Game in PYTHON ➤ https://l24.im/W8o
How to install Pyqt5 in Python? ➤ https://l24.im/jPVh
#python #pythondesktopapp
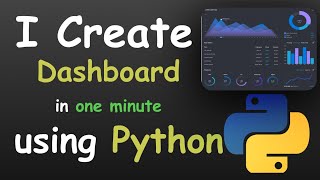
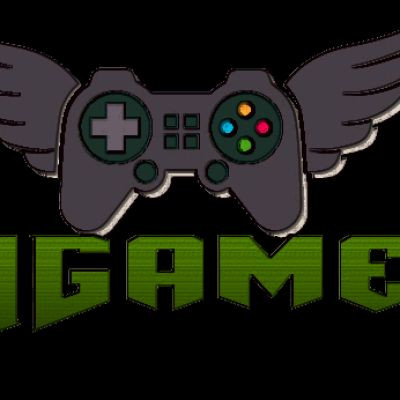
I Create Dashboard in One Minute using Python | Python for beginners | #python #coding #programming
In this video, you'll learn how to build a simple and interactive dashboard using Python and the Dash framework. Dash is a powerful tool for creating dynamic web applications, and in this tutorial, we'll go step-by-step through the process of setting up a dashboard, visualizing data, and making it interactive.
🔧 What you'll learn:
Setting up Dash in Python
Creating interactive charts and graphs
Visualizing data using Plotly
Adding dynamic user input with callbacks
Building a clean, responsive dashboard layout
📚 Libraries used:
Dash
Plotly
Pandas
💡 Sample project covered: A basic dashboard that visualizes data on different fruit sales across cities. This simple project will help you understand how to build real-world applications with Dash!
🚀 By the end of this tutorial, you'll be able to:
Create a full-featured web dashboard with Python
Customize and style your dashboards for different use cases
Understand how to make data interactive using callbacks in Dash
🔔 Don't forget to subscribe for more Python tutorials, and let me know in the comments what dashboard features you'd like to see in future videos!
Check out the Wireless Mouse 👇 :
https://amzn.to/409mowK
Check out the Apple Headphones 👇:
https://amzn.to/3Y89RXP
Check out the leather jacket here 👇:
https://amzn.to/480xgyT
Practice Python Quizes 👇:
https://quizbyte.vercel.app/
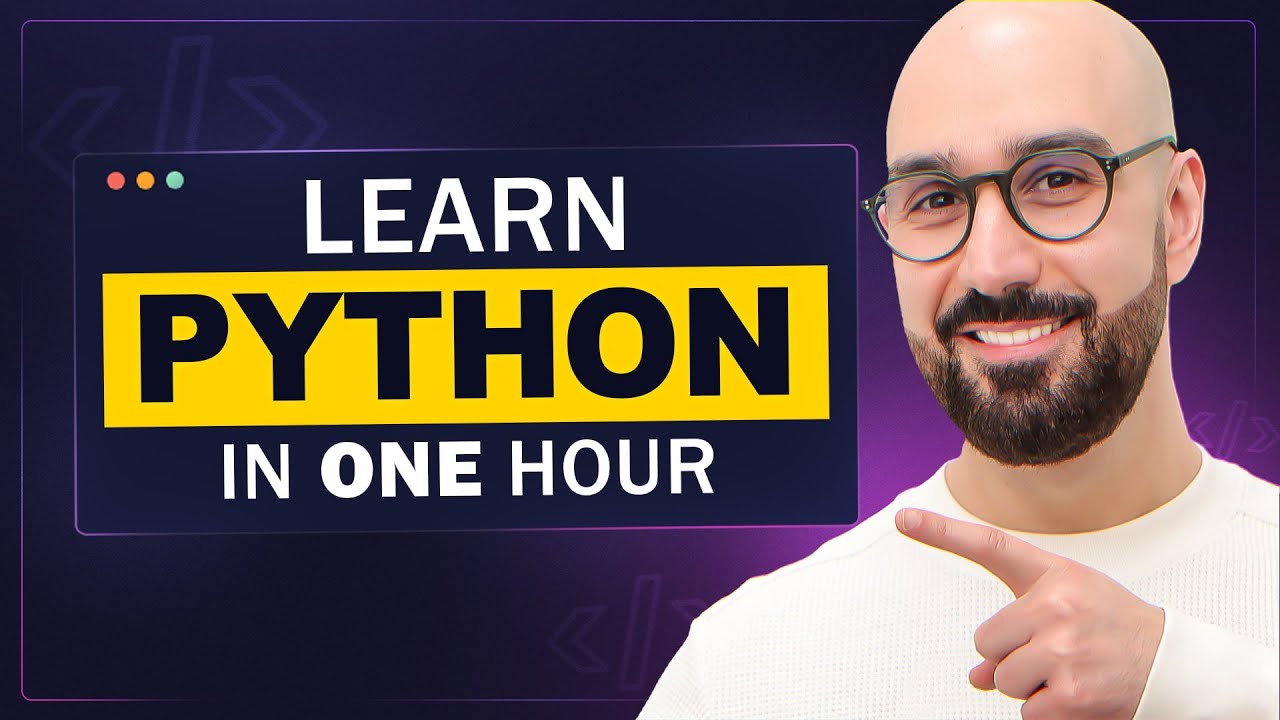
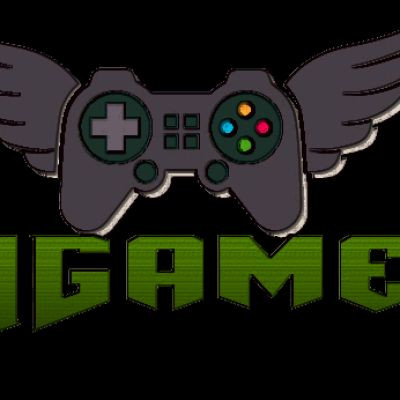
Learn Python basics in 1 hour! ⚡ Get 6 months of PyCharm FREE with the coupon in the description!
🚀 Want to dive deeper? Check out my Python mastery course:
- English edition: https://mosh.link/python-course
- Hindi (हिन्दी) edition: https://mosh.link/python-course-hindi
- Subscribe for more Python tutorials like this: https://goo.gl/6PYaGF
📕 Get the FREE goodies:
- Python cheat sheet: https://mosh.link/python-cheatsheet
- Get 6 months of PyCharm for free with this coupon code: MOSH_YOUTUBE - Redeem it at: https://jb.gg/redeem
✋ Stay connected:
- Twitter: https://twitter.com/moshhamedani
- Facebook: https://www.facebook.com/programmingwithmosh/
- Instagram: https://www.instagram.com/codewithmosh.official/
- LinkedIn: https://www.linkedin.com/school/codewithmosh/
⭐ Related tutorials
https://youtu.be/yVl_G-F7m8c?si=11emtFyDccTKCGn7
📖 TABLE OF CONTENT
0:00:00 Introduction
0:00:30 What You Can Do With Python
0:01:15 Your First Python Program
0:05:30 Variables
0:09:08 Receiving Input
0:10:48 Type Conversion
0:18:49 Strings
0:23:41 Arithmetic Operators
0:25:59 Operator Precedence
0:27:11 Comparison Operators
0:28:52 Logical Operators
0:31:06 If Statements
0:36:16 Exercise
0:41:42 While Loops
0:45:11 Lists
0:48:47 List Methods
0:52:16 For Loops
0:54:54 The range() Function
0:57:43 Tuples
#Python #AI #MachineLearning #WebDevelopment
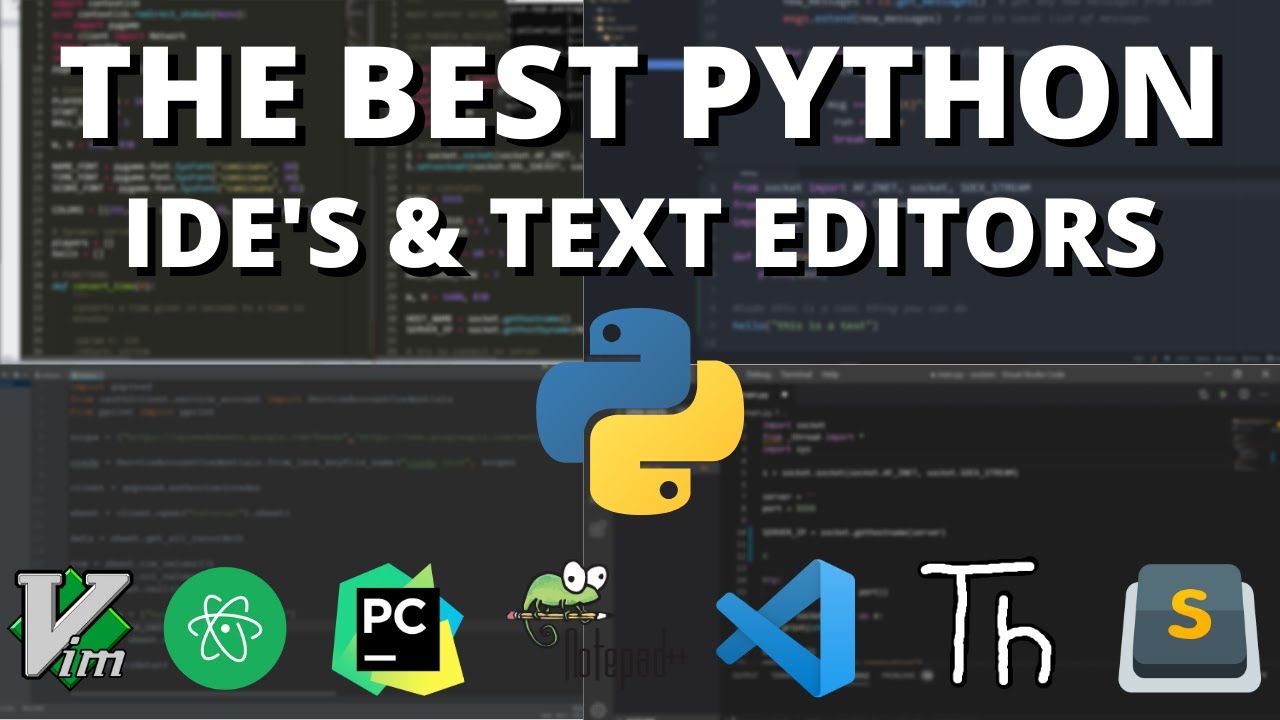
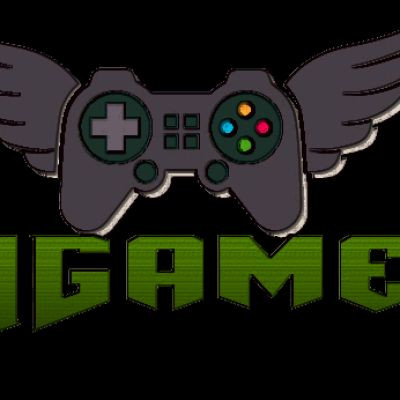
In this video I'll be showcasing the best python editors and ides. These software tools help to speed up your coding and come with a ton of useful features. Each python IDE and editor on this list has its pros and cons and different use cases associated with it. Do you agree with my list? Let me know!
⭐️ Thanks to Kite for sponsoring this video! Download the best AI automcolplete for python programming for free: https://kite.com/download/?utm_medium=referral&utm_source=youtube&utm_campaign=techwithtim&utm_content=top-5-ide-python
📝 Editors Featured
⌨ Vim: https://www.vim.org/download.php
⌨ Atom: https://atom.io/
⌨ VsCode: https://code.visualstudio.com/
⌨ Sublime: https://www.sublimetext.com/
⌨ PyCharm: https://www.jetbrains.com/pycharm/
◾◾◾◾◾
💻 Enroll in The Fundamentals of Programming w/ Python
https://tech-with-tim.teachabl....e.com/p/the-fundamen
📸 Instagram: https://www.instagram.com/tech_with_tim
🌎 Website https://techwithtim.net
📱 Twitter: https://twitter.com/TechWithTimm
⭐ Discord: https://discord.gg/pr2k55t
📝 LinkedIn: https://www.linkedin.com/in/tim-ruscica-82631b179/
📂 GitHub: https://github.com/techwithtim
🔊 Podcast: https://anchor.fm/tech-with-tim
💵 One-Time Donations: https://www.paypal.com/donate/?token=m_JfrPK7DsK4PLk0CxNnv4VPutjqSldorAmgQIQnMozUwwQw93vdul-yhU06IwAuig15uG&country.x=CA&locale.x=
💰 Patreon: https://www.patreon.com/techwithtim
◾◾◾◾◾◾
⚡ Please leave a LIKE and SUBSCRIBE for more content! ⚡
⭐ Tags ⭐
- Tech With Tim
- Python Tutorials
- Best Python IDE
- Best Python Code Editor
- Top Editor/IDE Python
- Python Best IDE's
⭐ Hashtags ⭐
#Python
![The Complete App Development Roadmap [2024]](https://i.ytimg.com/vi/yye7rSsiV6k/maxresdefault.jpg)
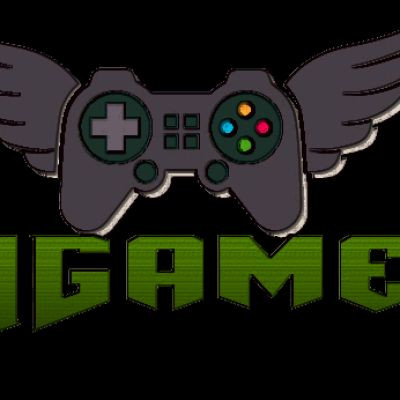
Go from zero to a mobile app developer in 12 months. This step-by-step roadmap covers the essential skills and latest technologies to become an app developer in 2024.
Download the FREE roadmap PDF here: https://mosh.link/mobile-roadmap
✋ Stay connected
- Complete courses: https://codewithmosh.com
- Twitter: https://twitter.com/moshhamedani
- Facebook: https://www.facebook.com/programmingwithmosh/
- Instagram: https://www.instagram.com/codewithmosh.official/
- LinkedIn: https://www.linkedin.com/school/codewithmosh/
🔗 Other roadmaps
https://youtu.be/Tef1e9FiSR0?si=QpVnZ_o9-DAXzT71
https://youtu.be/OeEHJgzqS1k?si=qd0ZIqAzUpZQn6BX
📚 Tutorials
https://youtu.be/W6NZfCO5SIk?si=yS0lQXyy3qwQF3DA
https://youtu.be/8JJ101D3knE?si=OGTuS35LQqSunuhh
https://youtu.be/BBpAmxU_NQo?si=dm-ZCPxVBYWS1Qhn
https://youtu.be/NU_1StN5Tkk?si=gsMONPdgxouQOolu
https://youtu.be/SqcY0GlETPk?si=O93IXejTVuh_5cbY
https://youtu.be/0-S5a0eXPoc?si=yP7qia07NN2FMeS2
📖 Chapters
00:00 - Introduction
00:08 - Native vs Cross-platform Development
04:08 - Languages
04:57 - Version control (Git)
05:25 - Data structures & algorithms
06:12 - Design patterns
07:14 - Mobile frameworks
#appdevelopment #coding #programming
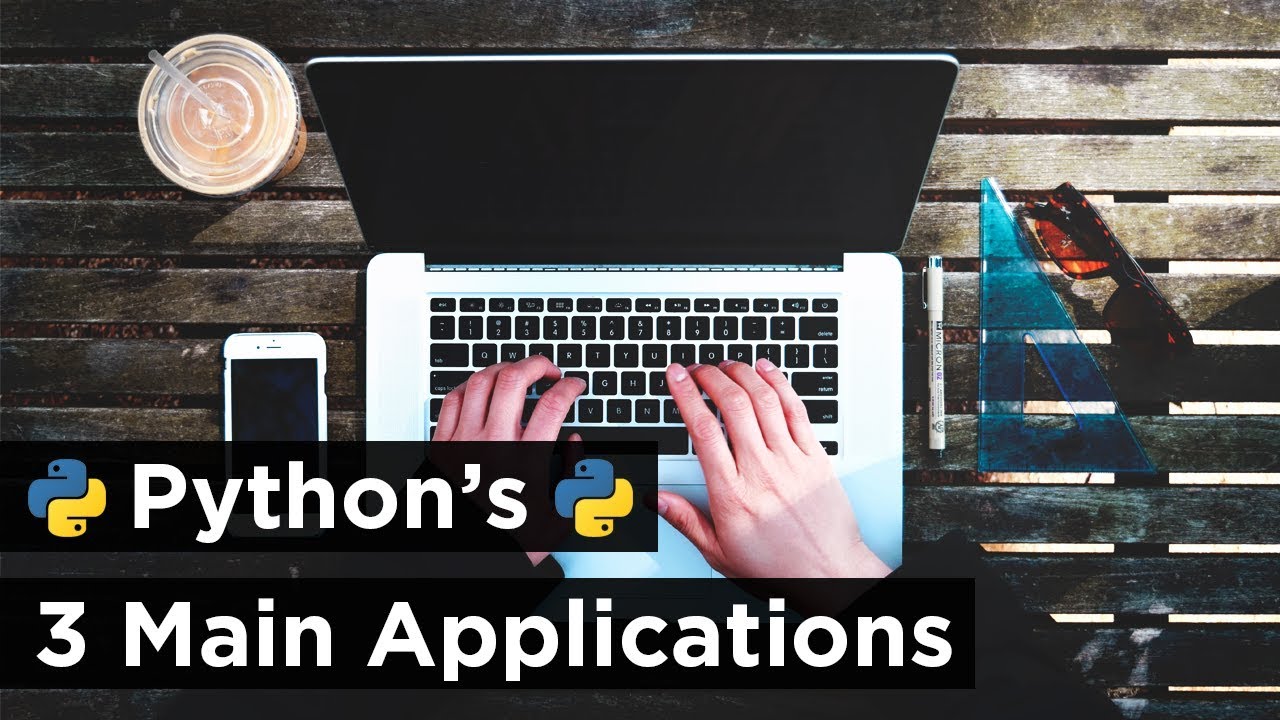
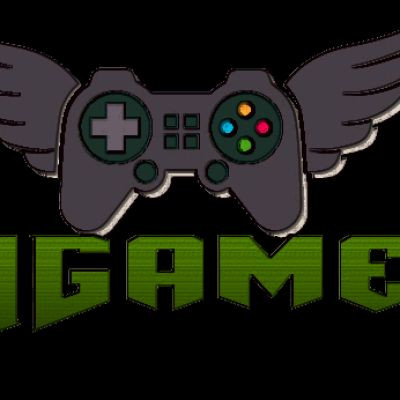
What is Python used for? What can you do with Python? Watch this video to find out :)
Looking for a Python tutorial for beginners? I have a playlist for that here: https://www.youtube.com/playli....st?list=PLBZBJbE_rGR
Also, if you're looking for a good Django tutorial, I recommend the book called Django for Beginners. You can find it here: http://csdojo.io/dj
You can also find the free sample chapters of that book here: https://djangoforbeginners.com/
And, you should follow me on Twitter: https://twitter.com/ykdojo
Instagram: https://www.instagram.com/ykdojo/
Or Facebook: https://www.facebook.com/entercsdojo
Links I mentioned in the video:
- frontend vs backend (my explanation): https://bit.ly/2tlSqp4
- Flask vs Django: https://goo.gl/QY4W4a
- My data visualization tutorial video: https://youtu.be/a9UrKTVEeZA
- The quora thread about desktop applications: https://goo.gl/jMX3eU
Outline (check the comment section for a clickable version):
0:44 : Web development intro
1:08 : Why web framework?
1:28 : Which Python web framework should you use?
2:30 : Machine learning intro - what is machine learning?
4:36 : Machine learning with Python
5:10 : How to learn machine learning
5:33 : Data analysis / visualization - an example
7:23 : Data analysis / visualization with Python
8:14 : Scripting - what is it?
9:20 : What about game development?
9:50 : What about desktop applications?
10:48 : What about embedded applications?
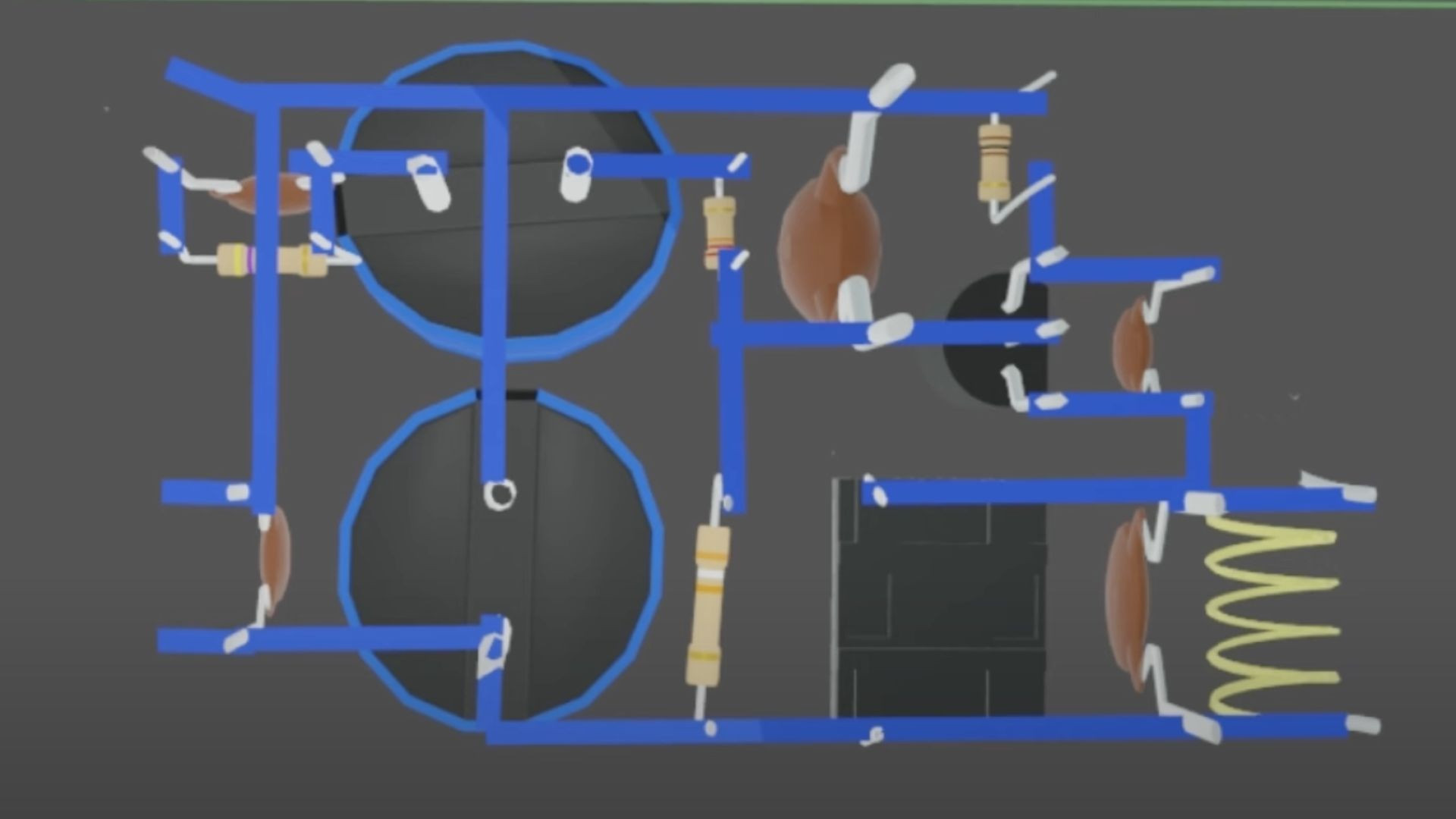
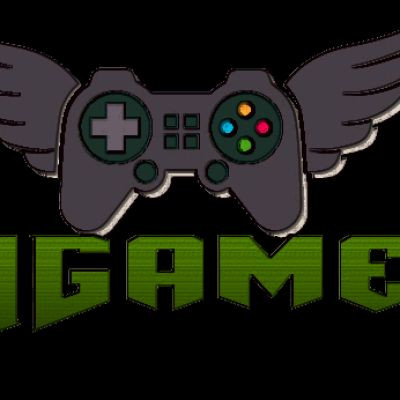
How to build an FM transmitter circuit. A complete build from beginning to end including all parts, components and tools needed. FM radio station transmitter for home use. Have your friends and family hear you on the radio with this great affordable easy to build transmitter. If you don't have a printed circuit board and want to know how to make a fm transmitter on breadboard then this circuit can work for you. Even if you are just interested in amateur radio or HAM radio as it's known this is a great way to learn about transmitters.
#fmtransmitter #fmradio #electronics #electroniccircuits
If you want to build your own home FM radio station then this is the right circuit. With a good signal range and strength and clear audio. This is a great DIY FM transmitter for lovers of electronic kits and amateur radio. It might not be the best fm transmitter ever made but it is cheap and lots of fun. If you are studying electronics or just for fun you want to know how to make a fm transmitter then is a fun way to learn. One of the reasons to want to know how to make an fm transmitter is to try hearing your own voice on the radio and having friends and family at your house hear you as you present on radio. fm transmitter static is also something this transmitter can overcome because of it's substantially better range than a normal car FM transmitter. In fact apart from this being a mono transmitter it is probably the best car fm transmitter you can make. While it's not intended as professional wireless fm transmitter for car use it is certainly a more powerful and fun way to go. If you want to know how to test an fm transmitter the range is about the easiest test and this circuit will give you way more range than an MP3 transmitter for your car. If are not worried about the bluetooth aspect and want just wireless fm transmitter that is cheap and fun. Build fm transmitter with the basic components with no complicated circuit. Even though this is low power it's actually a long range fm transmitter when you extend the antenna. With the right antenna this circuit can reach a mile in open space like a farm or event grounds. The cool thing is that this is not big and actually a mini fm transmitter that can be used almost anywhere. The fm transmitter antenna is important as far as range goes. If you use the right fm transmitter antenna you can get more range out of this low power transmitter than a higher power fm transmitter. Some talk about the gold whole house fm transmitter antenna length which is actually simply the wavelength calculate from the FM frequency. This diy fm transmitter antenna is from a radio controlled toy but you can use a more sophisticated antenna.
Original YouTube Video: https://www.youtube.com/watch?v=X2ozDgBF6v w
Disclaimer: This video is for education and entertainment purposes only. The creator of this video and this YouTube channel do not take any responsibility for any loss or harm that comes from building or using this device. Make sure you know how to use electronic equipment such as a soldering iron and be aware of, and follow, safety guidelines. Building and/or using this device is at your own risk.
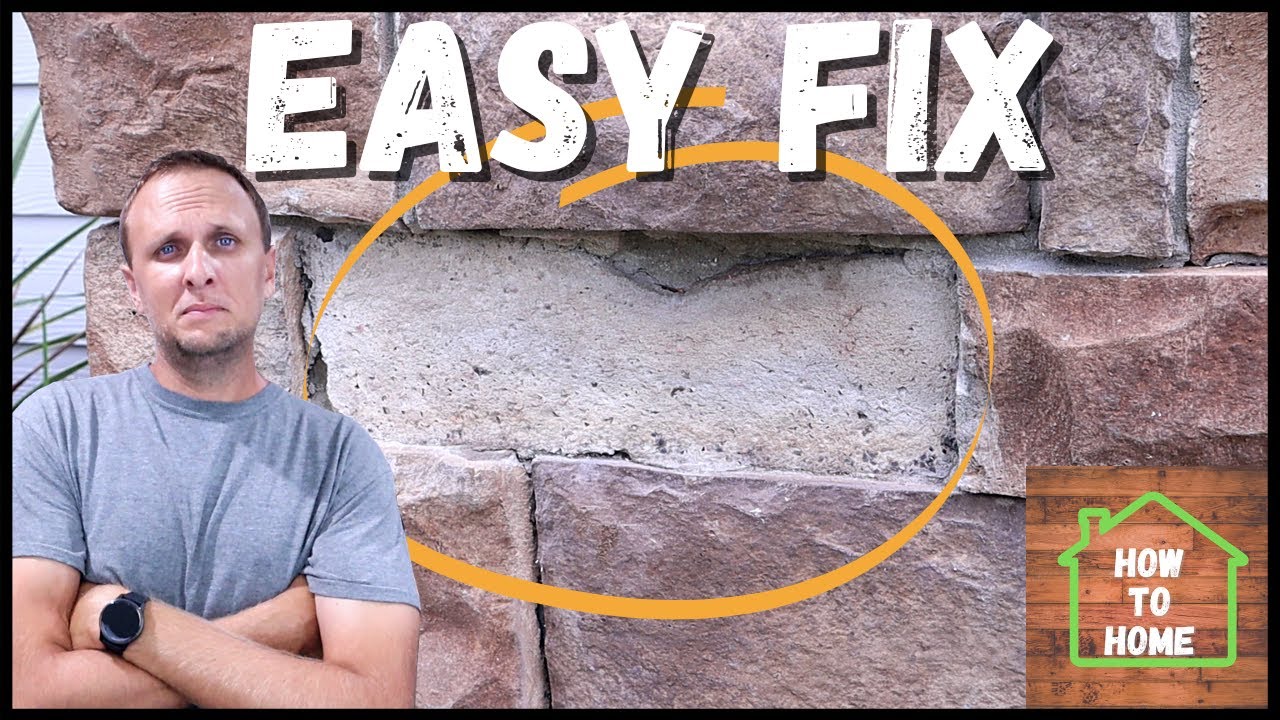
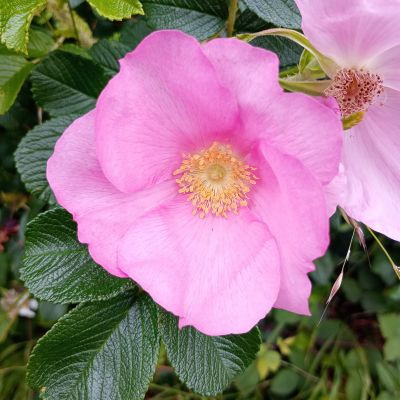
In this video I show you how to easily reattach stacked stone. Using the material in the link below and properly prepping the surface you can fix and repair stacked stone in minutes.
Loctite Landscape Adhesive: https://amzn.to/31xdmub
TSP Substitute: https://amzn.to/2HpJskF
Wire Brushes: https://amzn.to/37xxSP8
DISCLAIMER: Thank you for watching and for subscribing. You can support the channel at no cost to you by using one of the above affiliate links. This helps support the channel for new content!
Blessings,
Adam
How To Home assumes no liability for damage or injury. How To Home highly recommends using proper safety procedures and professionals when needed. No information contained in this video shall create any express or implied warranty or guarantee of any particular result. Any injury, damage or loss that may result from improper use of these tools, equipment, or the information contained in this video is the sole responsibility of the user and not How To Home. How To Home will not be held liable for any negligent or accidental damage or injury resulting from equipment, tools, electrical, fire, electronics or any items contained in this video. Attempt projects and repairs at your own risk.
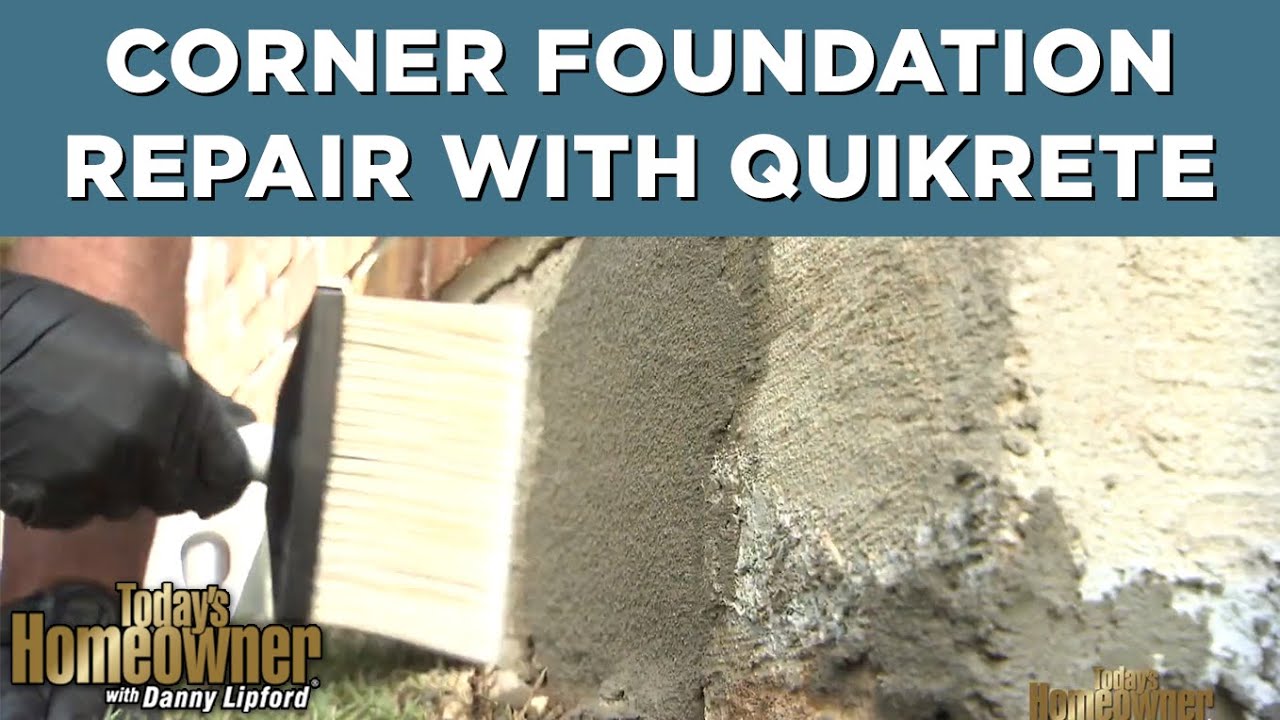
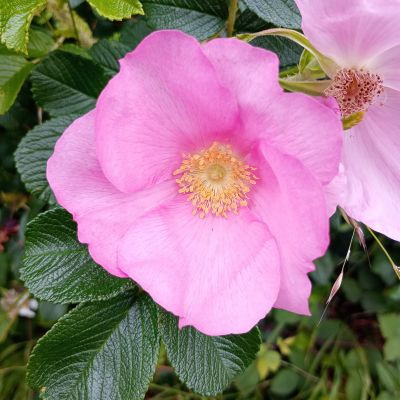
#diy #homeimprovement #houserepair
subscribe to Today's Homeowner for more great home improvement videos: https://pixelfy.me/SubscribeTodaysHomeowner
Today’s Homeowner Television is the highest-rated, Emmy-nominated home improvement TV show syndicated in the U.S., reaching more than 2 million weekly viewers with fresh, practical and trusted advice for maintaining and improving homes. In its 24th season, Today’s Homeowner is the second-longest syndicated running home improvement show in the U.S., hosted by the exclusive father-daughter team of Danny Lipford and Chelsea Lipford Wolf.
Visit Today's Homeowner: https://todayshomeowner.com/
Instagram: https://www.instagram.com/todayshomeowner/
Facebook: https://www.facebook.com/todayshomeownermedia/
Pinterest: https://www.pinterest.com/todayshomeowner/
Twitter: https://twitter.com/DannyLipford
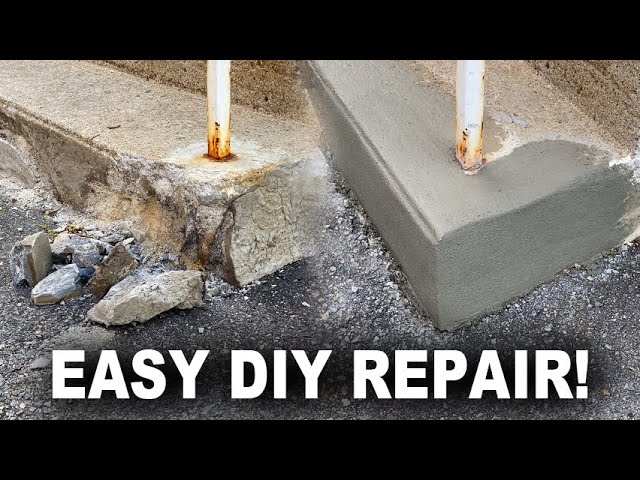
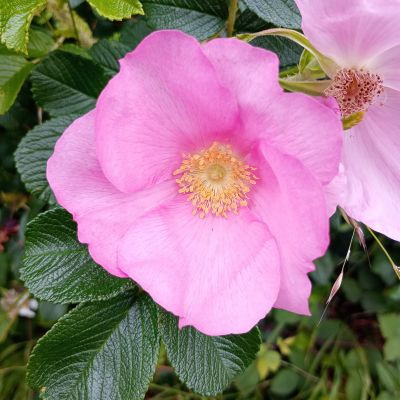
In this video I show you how to easily repair broken concrete stairs with Quikcrete quick-setting cement.
Items I used for this repair:
Tapcon Screws - https://amzn.to/3aGWLsj
Drill bit - https://amzn.to/3nph17a
Cement - https://amzn.to/3t4ux1m
Bonding Adhesive - https://amzn.to/3UL1Cxs
Drill - https://amzn.to/3nt7pIH
Wire Brush - https://amzn.to/2PrRnC2
Trowel - https://amzn.to/3tZwgWU
Cold Chisels - https://amzn.to/3aKKXFy
Sponge - https://amzn.to/32TQ8yH
My Favorite Hammer EVER! - https://amzn.to/3eDEY6C
(Affiliate Links)
Facebook - http://bit.ly/FixerFacebook
Instagram - http://bit.ly/FixerInsta
Twitter - http://bit.ly/FixerTwitter
Buy some “The Fixer” merchandise here - http://bit.ly/FixerTS
Patreon - http://bit.ly/FixerPatreon
Check out my Amazon storefront to buy some of my favorite tools - http://bit.ly/FixerStore
My YouTube gear:
GoPro Hero 8 - https://amzn.to/2Xvj2l9
DJI Osmo Action Camera - https://amzn.to/2Xbp9OB
iPhone 12 - https://amzn.to/38VlzLI
iPad air 2 - https://amzn.to/2Vw04fQ
iPad camera mount - https://amzn.to/2V0gE8a
Canon 7d - https://amzn.to/2FANWRD
Lav microphone - https://amzn.to/2UZHe19
Camera tripod - https://amzn.to/2DwMzC7
Drograce action camera - https://amzn.to/2XOZFCt
Editing software (Adobe Premiere) - https://amzn.to/2VuVZsa
Adobe Photoshop - https://amzn.to/2DApNcT
Lighting Kit - https://amzn.to/2XGHuTq
(affiliate links)
DISCLAIMER: This video and description contains affiliate links, which means that if you click on one of the product links, I will receive a small commission. This helps support this channel and allows me to continue to make videos like this. Thank you for your support!
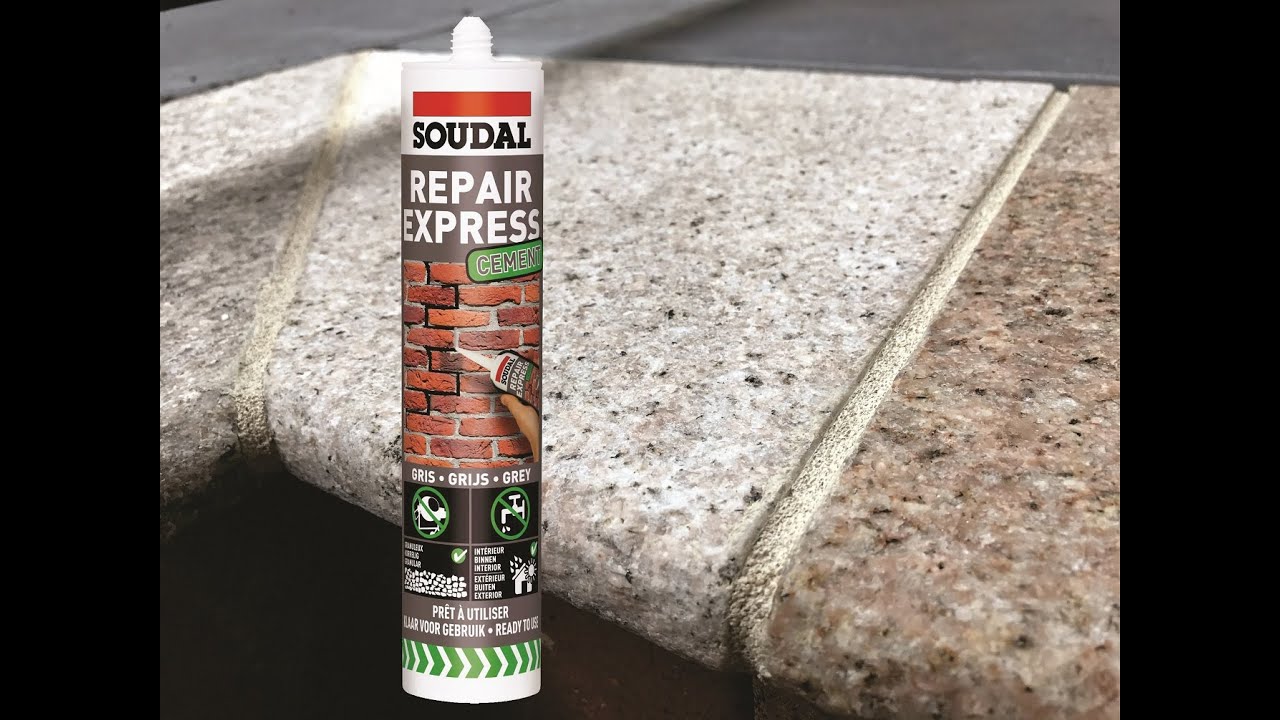
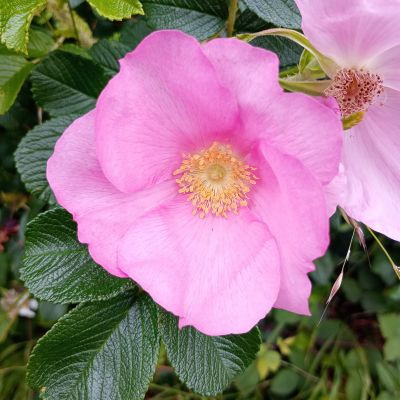
Repair Express Cement is a high quality filler with granular structure that can be used for repairing holes and cracks in concrete and cement. It has very good adhesion to all common porous surfaces and shrink free repairing of cracks and joints in concrete. Available in 2 colours (Grey and Beige). Visit https://soudal.com.au/productl....ist/fillers/repairex for more details.
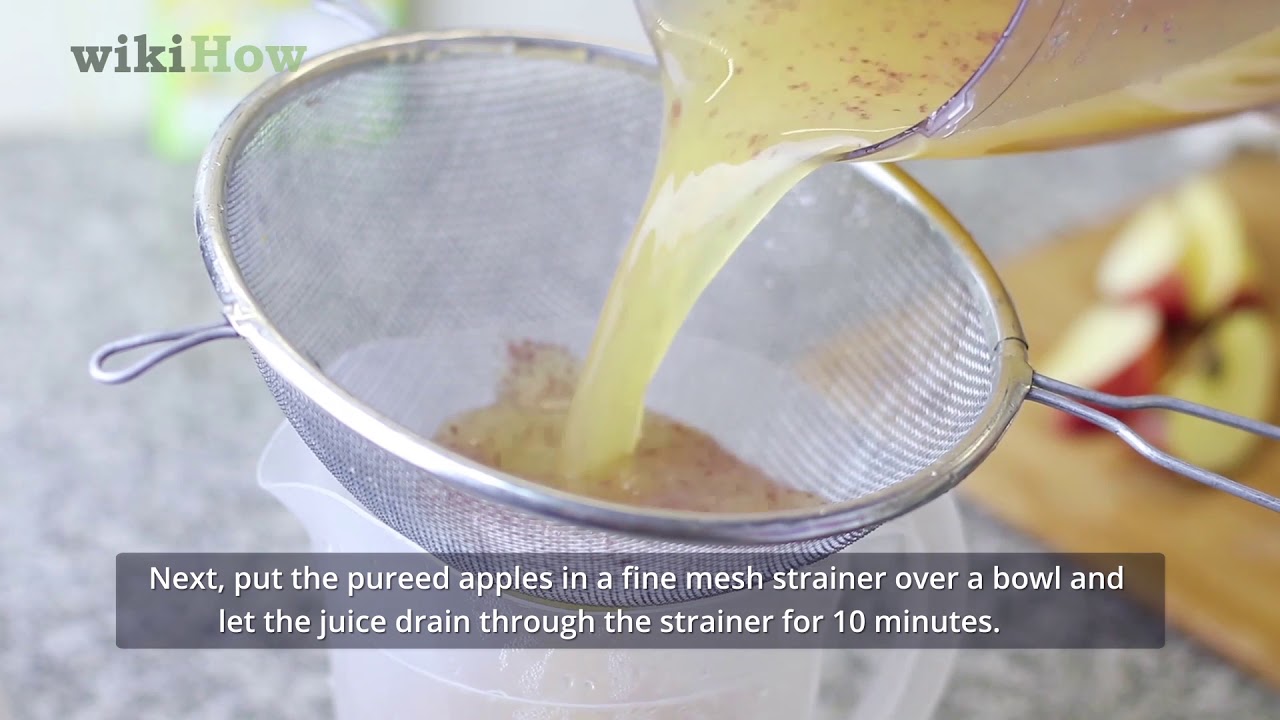
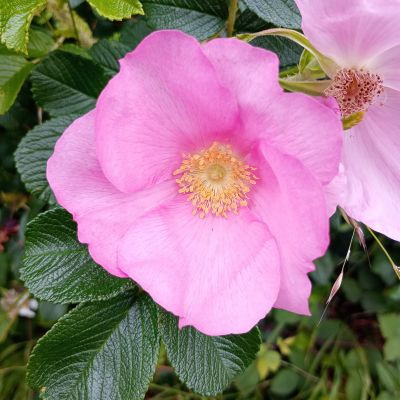
Learn how to make apple juice with this guide from wikiHow: https://www.wikihow.com/Make-Apple-Juice
Follow our social media channels to find more interesting, easy, and helpful guides!
Facebook: https://www.facebook.com/wikiHow/
Twitter: https://twitter.com/wikiHow
Instagram: https://www.instagram.com/wikihow/