Cách tạo kiểu
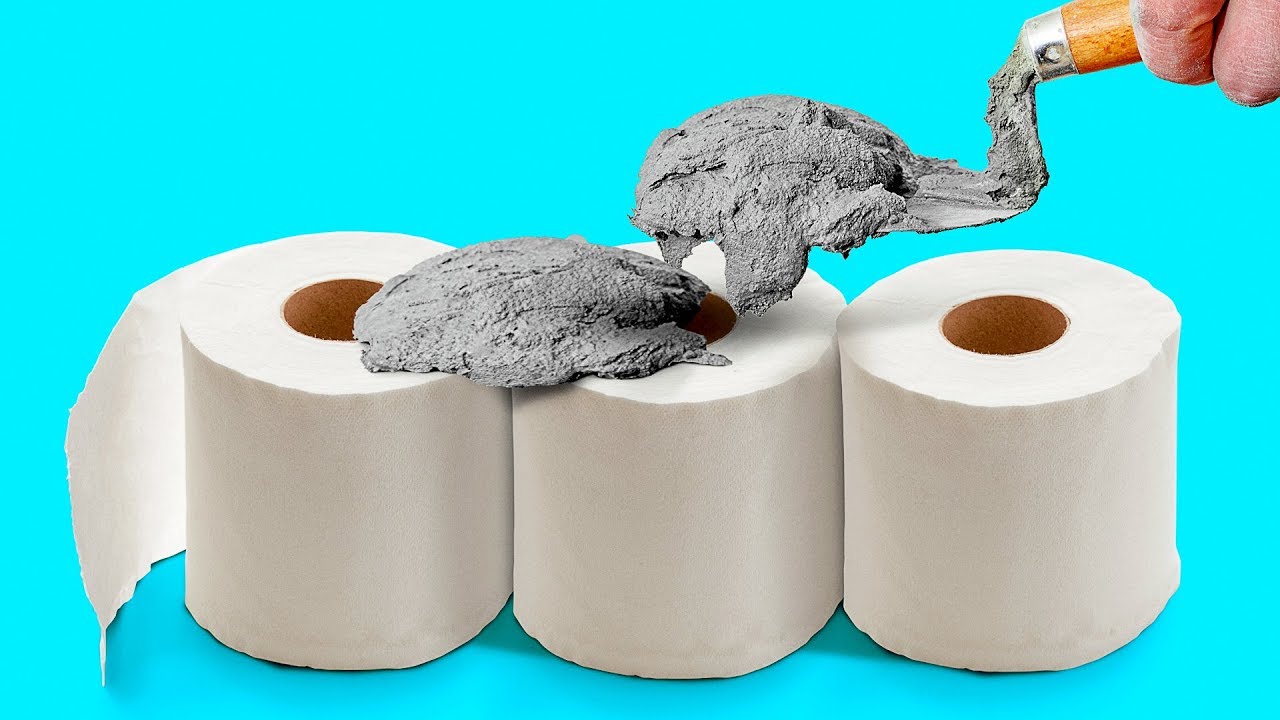
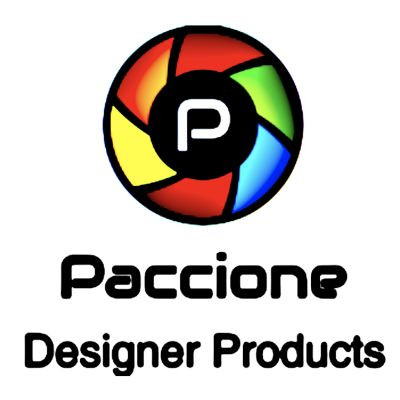
Upgrade your apartment with these easy DIY ideas
Does your room seems boring to you? Don't worry, we've got it covered! Here are some crazy cool crafts and DIYs that will definitely leave you inspired. Just prepare some cement and polymer clay.
DIY lamp stand
If even Ikea lamp stands look boring to you, it is time to create something unique. Take 10-12 old books that you won't read anymore and mix a bowl of cement. Put the books in the cement mixture one by one and then place them one on another randomly to create a column. Let dry. Well done! Now you can put your lamp on this unique handmade lamp stand that makes your room look so cozy :)
Easy planters
Do you like plants and flowers in your house? So do we! However, common planters may look boring. Here is a simple DIY idea for you. Take a pair of rubber gloves for cleaning and fill them in with some cement. Put both gloves in a big bowl to create a round shape and let dry. Carefully cut off and remove the gloves. Fill the cement hands with ground ans plant your favorite flowers. By the way, it can be a really nice gift idea for your family and friends.
Watch the video for more DIY cement home decor ideas.
Timestamps:
00:47 DIY lamp stand from old books
02:38 An easy and lovely way to reuse old light bulbs
05:25 Cute little candle holders
07:10 Amazing garden decor from old toys
10:29 Handmade polymer clay ideas
----------------------------------------------------------------------------------------
Our Social Media:
Facebook: https://www.facebook.com/5min.crafts/
Instagram: https://www.instagram.com/5.min.crafts/
Twitter: https://twitter.com/5m_crafts
Subscribe to 5-Minute Crafts GIRLY: https://goo.gl/fWbJqz
Subscribe to 5-Minute Crafts KIDS: https://goo.gl/PEuLVt
Subscribe to 5-Minute Crafts MEN: http://bit.ly/2S69VUG
The Bright Side of Youtube: https://goo.gl/rQTJZz
----------------------------------------------------------------------------------------
For more videos and articles visit:
http://www.brightside.me
Music by Epidemic Sound: https://www.epidemicsound.com/ This video is made for entertainment purposes. We do not make any warranties about the completeness, safety and reliability. Any action you take upon the information on this video is strictly at your own risk, and we will not be liable for any damages or losses. It is the viewer's responsibility to use judgment, care and precautions if one plans to replicate.
The following video might feature activity performed by our actors within controlled environment- please use judgment, care, and precaution if you plan to replicate.
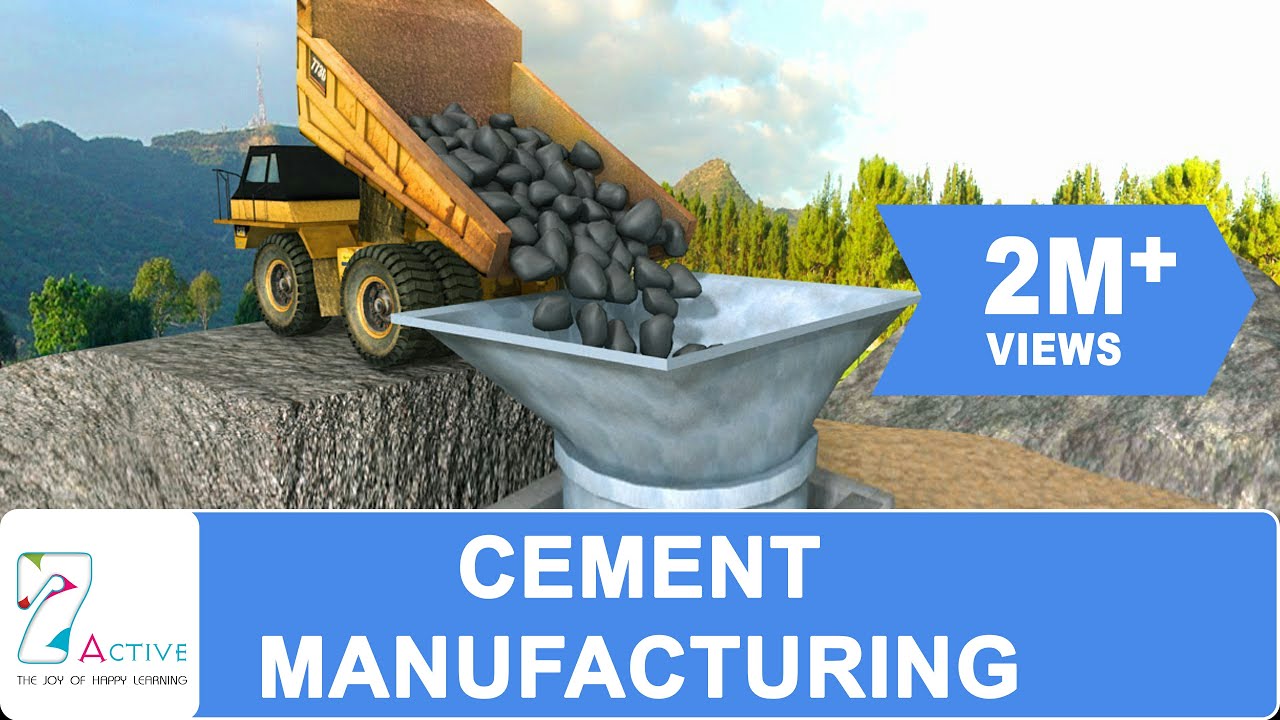
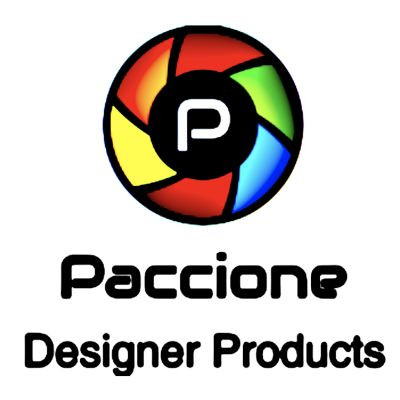
#cement #manufacturing
Follow us: https://www.instagram.com/7activestudio/
For more information:
www.7activestudio.com
7activestudio@gmail.com
Contact: +91- 9700061777, 040-66564777
7 Active Technology Solutions Pvt.Ltd. is an educational 3D digital content provider for K-12. We also customise the content as per your requirement for companies platform providers colleges etc . 7 Active driving force "The Joy of Happy Learning" -- is what makes difference from other digital content providers. We consider Student needs, Lecturer needs and College needs in designing the 3D & 2D Animated Video Lectures. We are carrying a huge 3D Digital Library ready to use.
Voice Over Credit: Muls N Ravs Entertainment Pvt. Ltd. (www.mulsnravs.com)

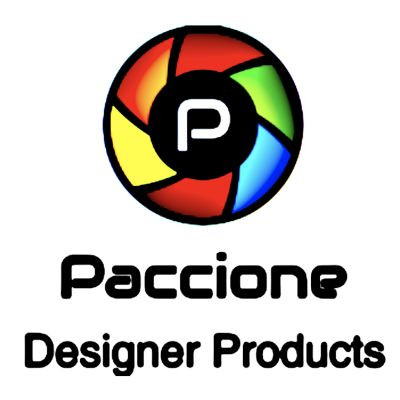
*WE HAD A MASSIVE DRIVEWAY POUR IN THE FRONTYARD THIS DAY WHICH IS WHY THERE WAS SO MANY GUYS* In this video we show you how to pour your basic 16 x 12 Concrete Slab! We go over all the necessary steps for your concrete slab to come out perfect! We show you how to form the slab, put rebar in at 2ft x 2ft centers, rod it, bull float it, put joints in, edge it, use the fresno/Big Blue and broom it. We hope you find this information Valuable and to help you on your next project! If there are any questions please dont hesitate to comment below and dont forget to like share ans subscribe! It helps motivate us to teach and bring more videos to all of you knowing these videos help! Thank you all for your support!
OFFICIAL INSTAGRAM - https://www.instagram.com/odellconcrete/
Website: http://DavidOdellConcrete.com
David Odell's Store: odellcompleteconcrete.com

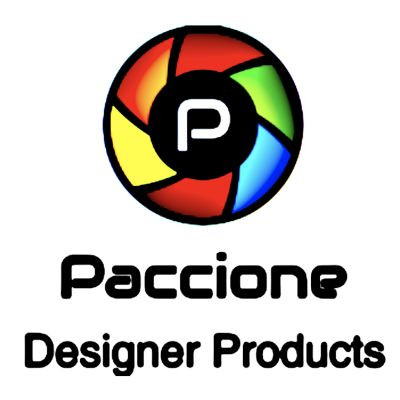
Primitive Technology: Wood Ash Cement - Creating wood ash cement from scratch
Subscribe: http://bit.ly/subPT | Never miss a video! Enable ‘ALL’ Notifications!
More videos, watch me cultivate and cook yams from scratch: http://bit.ly/2L5HmqY
Follow Primitive Technology:
Wordpress: https://primitivetechnology.wordpress.com/
Patreon: https://patreon.com/user?u=2945881
Watch More Primitive Technology:
Latest Uploads: https://youtube.com/playlist?l....ist=PLGnWLXjIDnpBR4x
Pyrotechnology: https://youtube.com/playlist?l....ist=PLGnWLXjIDnpBVRq
Shelter: https://youtube.com/playlist?l....ist=PLGnWLXjIDnpBBsd
Weapons: https://youtube.com/playlist?l....ist=PLGnWLXjIDnpA-XG
Popular Videos: https://youtube.com/playlist?l....ist=PLGnWLXjIDnpAb29
Partial credit for this idea goes to James Keane who I discussed this with on my wordpress site (see conversation): https://primitivetechnology.wordpress.com/2018/03/06/lime/#comment-9736
I developed an experimental cement from made only from re-fired wood ash as its cementitious material. It was mixed with crushed terracotta as an aggregate and formed into a cube. The cement set hard after 3 days and did not dissolve in water after this period.
Process: First I burnt bark and leaves in a kiln at high temperatures to produce well burnt, mostly white wood ash. The ash was then mixed into water and stirred well. The excess water was poured off and the resulting paste was made into pellets and allowed to dry. A pellet was then re-heated in the forge until it glowed about orange hot. This was then taken out, cooled and dropped in a pot of water. The pellet dissolved and boiled due to a chemical reaction with the water. The paste was stirred and crushed terracotta (old tiles from previous projects) was added and mixed to form a mouldable mortar. This was formed into a cube and allowed to set for three days (in the video, a cube made exactly the same way 3 days previously was used due to time constraints). The resultant cube was strong and made a slight ringing sound when tapped with a finger nail. It was placed in water for 24 hours to simulate a very heavy rain event and did not dissolve or release residues into the water.
My current theory: The main component of wood ash consists of calcium in some form (e.g. calcium carbonate, calcium oxide). This can be up to 45% from my research. Calcium is in higher concentration in the bark and leaves of a tree. When the ash is mixed with water, the soluble component of wood ash (10% pot ash) dissolves into the water. But seeing that it does nothing for the cementing process, it is drained off leaving the insoluble calcium (and other components) in the paste. Doing this probably raises the relative percentage of calcium in the paste to about 50% or more. Most of the other 50 % consists of silica and alumina which are pozzolans, materials that chemically react with calcium hydroxide to increase the durability of the cement product. The paste was then made into a pellet and fired again to high temperature to convert all the calcium compounds to calcium oxide. It also reduces any charcoal in the pellet to ash if it hadn’t already been burnt the first time. This step seemed important as un-fired ash pellets only partially hardened and would fall apart in water, though retaining a weak undissolved 5mm thick crust. I can only surmise that re-firing the ash just gave a greater conversion of the calcium components to calcium oxide. The pellet is slaked in water converting the calcium oxide to calcium hydroxide. This cement was mixed with crushed terracotta which may also help in some way that I’m not aware of as I only did this one experiment and did not test other aggregates yet (e.g. sand, gravel etc.). Terracotta is porous and might hold together better than other materials. The mixture is allowed to set in air where carbon dioxide reacts with calcium hydroxide to form calcium carbonate cementing the aggregate together. After this, the cement will not dissolve in water.
Use: I think this material might have a potential use as a mortar holding rocks or bricks together in wet environments where limestone or snail shells are unavailable for making cement. Wood ash is a pretty ubiquitous material to most natural environments inhabited by people using biomass fuels. Wood ash cement turns a waste product into a valuable building material. From my research, wood ash is already being used as a partial replacement for cement in the building industry without decreases in strength of the final product. But I’ve only just started experimenting with it and don’t know its full capabilities and limitations. Calcium content of wood ash differs depending on the species of tree, the part of the tree burnt and the soil it’s grown on. Cautious experimentation is still required before committing to a hut built from this material.
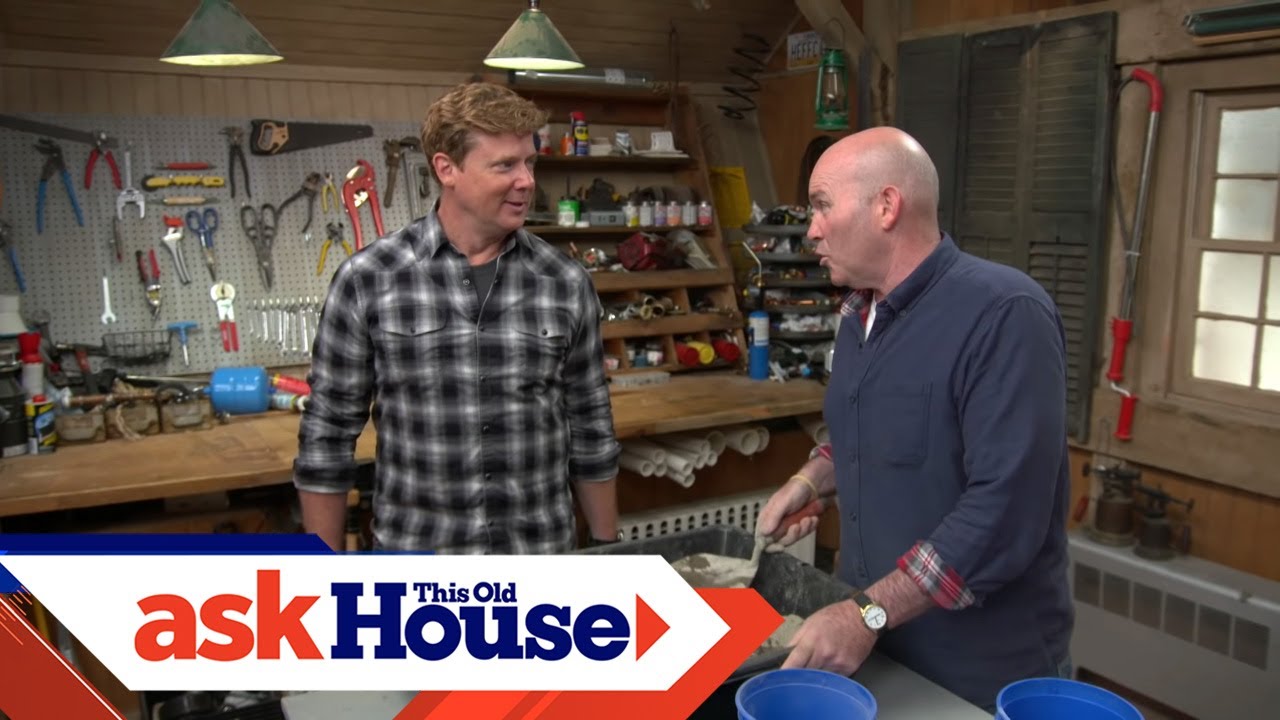
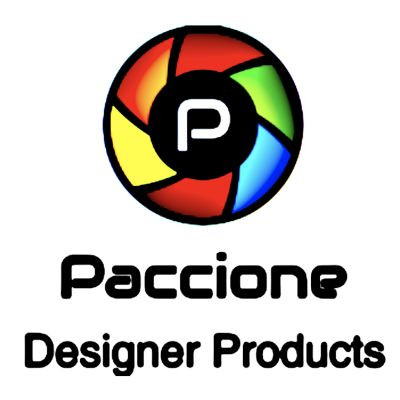
Ask This Old House mason Mark McCullough explains the basics of making concrete
SUBSCRIBE to This Old House: http://bit.ly/SubscribeThisOldHouse
Time: 10 minutes
Cost: $20
Skill Level: Beginner
Tools List for Making Concrete:
Trowel
Mixing bucket
Bucket for measuring
Shopping List:
Sand in bulk
Aggregate in bulk (crushed stone, etc.)
Portland cement in bulk
Steps:
1. Measure out each ingredient in the following proportion: 3 parts sand, 2 parts aggregate, 1 part Portland cement. Use a bucket to help keep the measurements accurate.
2. Pour the sand, aggregate, and Portland cement into a mixing bucket. To make the mix stronger, add more aggregate and Portland cement.
3. Add water slowly to the bucket and begin to mix it up with the trowel. Add more water as needed until the concrete is at the correct consistency.
Resources:
Most concrete can be made using a premixed bag, like the one Mark demonstrated, which is manufactured by Quikrete (https://www.quikrete.com/).
For bigger jobs that require a lot of concrete, it’s cheaper to make the concrete yourself. The sand, aggregate, and Portland cement can all be found at masonry yards.
Expert assistance with this segment was provided by MJM Masonry (http://mjmmasonry.com/).
About Ask This Old House TV:
Homeowners have a virtual truckload of questions for us on smaller projects, and we're ready to answer. Ask This Old House solves the steady stream of home improvement problems faced by our viewers—and we make house calls! Ask This Old House features some familiar faces from This Old House, including Kevin O'Connor, general contractor Tom Silva, plumbing and heating expert Richard Trethewey, and landscape contractor Roger Cook.
Follow This Old House and Ask This Old House:
Facebook: http://bit.ly/ThisOldHouseFB
Twitter: http://bit.ly/ThisOldHouseTwitter
http://bit.ly/AskTOHTwitter
Pinterest: http://bit.ly/ThisOldHousePinterest
Instagram: http://bit.ly/ThisOldHouseIG
http://bit.ly/AskTOHIG
Tumblr: http://bit.ly/ThisOldHouseTumblr
For more on This Old House and Ask This Old House, visit us at: http://bit.ly/ThisOldHouseWebsite
How to Make Your Own Concrete | Ask This Old House
https://www.youtube.com/user/thisoldhouse/

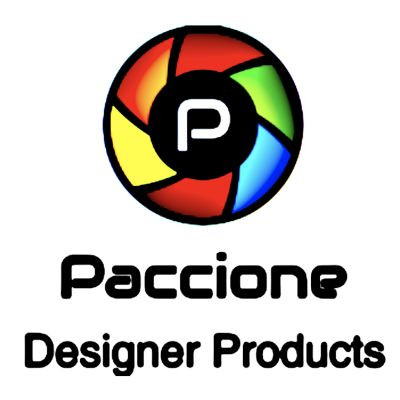
An Attempt at Reproducing Ancient Roman Concrete by using Limestone, Volcanic Ash and Aggregate. Please Hit The LIKE and SUBSCRIBE BUTTONS as well as the NOTIFICATION BELL. Feel Free to Check out my Amazon Influencer Page and Follow Me on Instagram, Facebook and Twitter. Thanks For Watching.
Amazon https://www.amazon.com/shop/corporalscorner?isVisitor=true&ref=exp_inf_own_pub_corporalscorner
Self-reliance Outfitters https://www.selfrelianceoutfit....ters.com/collections
Facebook https://www.facebook.com/pages..../Corporals-Corner/51
#corporalscorner #shawnkelly #campinginthewoods
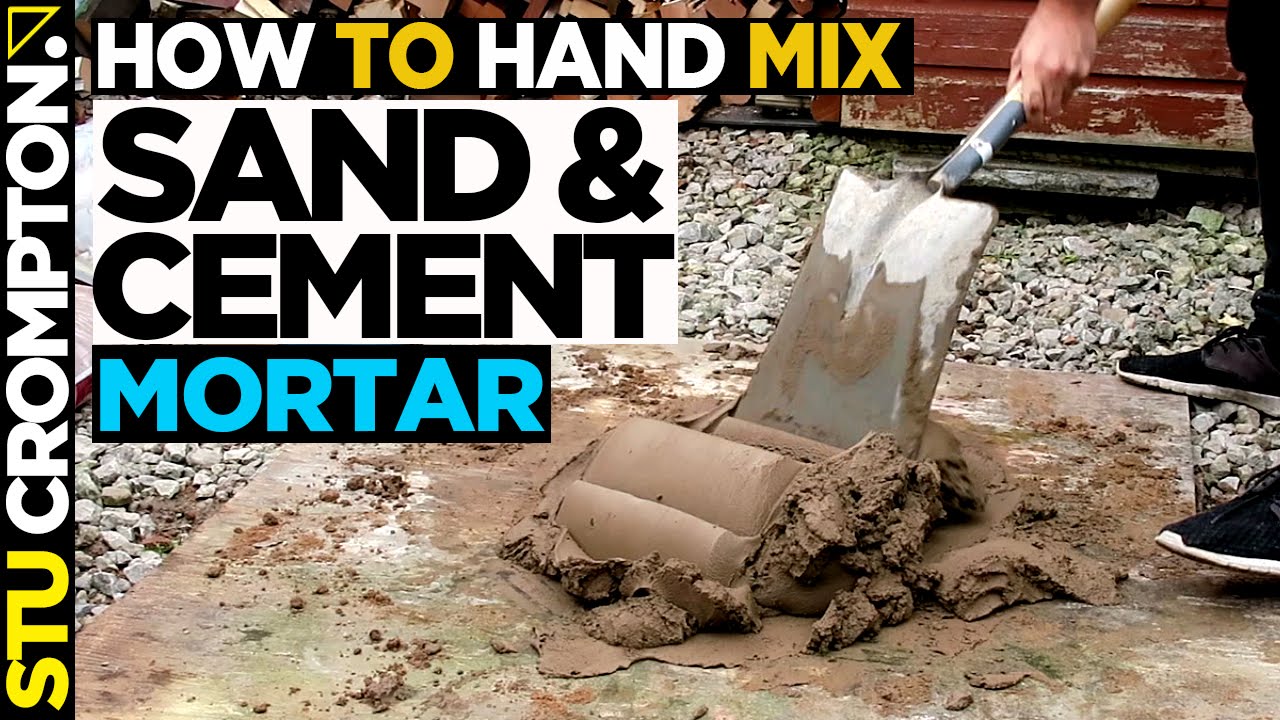
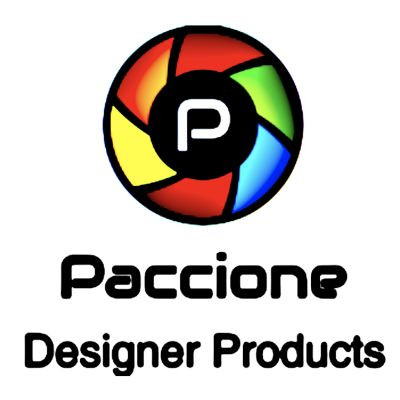
LEARN BRICKLAYING
Download My free bricklaying guide : https://courses.bestbricky.com..../4-Step-Bricklaying-
hope you enjoy :)
stu
please support my journey on this channel by becoming a patreon so i can keep producing content. https://www.patreon.com/stucrompton
every penny counts thankyou
My Aerial videography business www.skyawesome.co.uk
Twitter: https://twitter.com/stucrompton
Facebook: https://www.facebook.com/stucromptonyoutube
Instagram: http://instagram.com/stucrompton
SnapChat: stucrompton
Acting website : www.stucrompton.com
live streaming
Periscope: stucrompton
Blab: stucrompton
Meerkat: stucrompton
music from epedemicsound
songs used : making me feel alright
website here : http://www.epidemicsound.com/
Business: stucrompton@ymail.com
Thanks for watching!

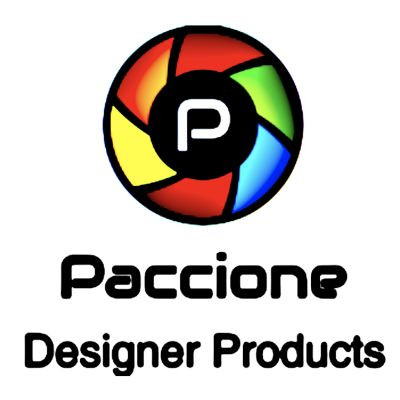
A cement is a binder, a substance used for construction that sets, hardens, and adheres to other materials to bind them together. Cement is seldom used on its own, but rather to bind sand and gravel (aggregate) together. Cement mixed with fine aggregate produces mortar for masonry, or with sand and gravel, produces concrete. Concrete is the most widely used material in existence and is behind only water as the planet's most-consumed resource.
Cement manufacturing is a complex process that begins with mining and then grinding raw materials that include limestone and clay, to a fine powder, called raw meal, which is then heated to a sintering temperature as high as 1450 °C in a cement kiln. In this process, the chemical bonds of the raw materials are broken down and then they are recombined into new compounds. The result is called clinker, which are rounded nodules between 1mm and 25mm across. The clinker is ground to a fine powder in a cement mill and mixed with gypsum to create cement. The powdered cement is then mixed with water and aggregates to form concrete that is used in construction.
Clinker quality depends on raw material composition, which has to be closely monitored to ensure the quality of the cement. Excess free lime, for example, results in undesirable effects such as volume expansion, increased setting time or reduced strength. Several laboratory and online systems can be employed to ensure process control in each step of the cement manufacturing process, including clinker formation.
🔰Recomended Videos:
https://youtu.be/K4Pvxzu6Hbs?si=KTxnp-e1T5dzHZkr
https://youtu.be/xieRUXbqKws?si=n2QtbSwE-twsZALe
https://youtu.be/3W16JxdGtZA?si=qPju8ZjQt04n5dDb
https://youtu.be/c1NtUtXcGeQ?si=dbpr2O7qtfaewZPF
https://youtu.be/DeTyuLYEN4g?si=HxZXzexU8euSNW39
https://youtu.be/iwgMl5sr1O4?si=wWtQz_bfAKmAMIp3
https://youtu.be/3gPf0Ki4ge8?si=MGSoG1xnGMPyuRbd
https://youtu.be/m4zTKRJK4TM?si=XFfiiUjMWzZo6Kez

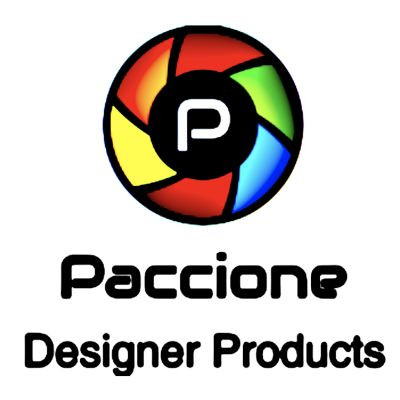
This experiment is not included in the MEL Chemistry subscription–we just love to show you the beauty of chemistry💙
For cool and safe experiments to do at home sign up to MEL Science here: https://goo.gl/ZK6dpv
It’s easy to make the simplest type of cement yourself. In this experiment, we’ll prepare a mixture which you can use to make a little house, for example for a dog.
Safety precautions
Wear a protective mask, gloves and glasses, and work in a well-ventilated room.
Warning! Only under adults supervision.
Reagents and equipment:
* building lime (calcium oxide, 100 g);
* sand (300 g);
* water (100-150 ml);
* deep container for mixing;
* trowel;
* bricks.
Step-by-step instructions
Mix the building lime with water. Gradually add sand and stir thoroughly. We get a simple cement mixture. Apply it to bricks and leave for a week. The bricks are stuck together!
Processes description
In the reaction of calcium oxide with water, calcium hydroxide forms.
СаО + Н₂О = Са(ОН)₂
In air, calcium hydroxide reacts with carbon dioxide with the formation of durable calcium carbonate, which envelops and sticks the sand particles together
Са(ОН)₂ + СО₂ = СаСО₃ + Н₂О
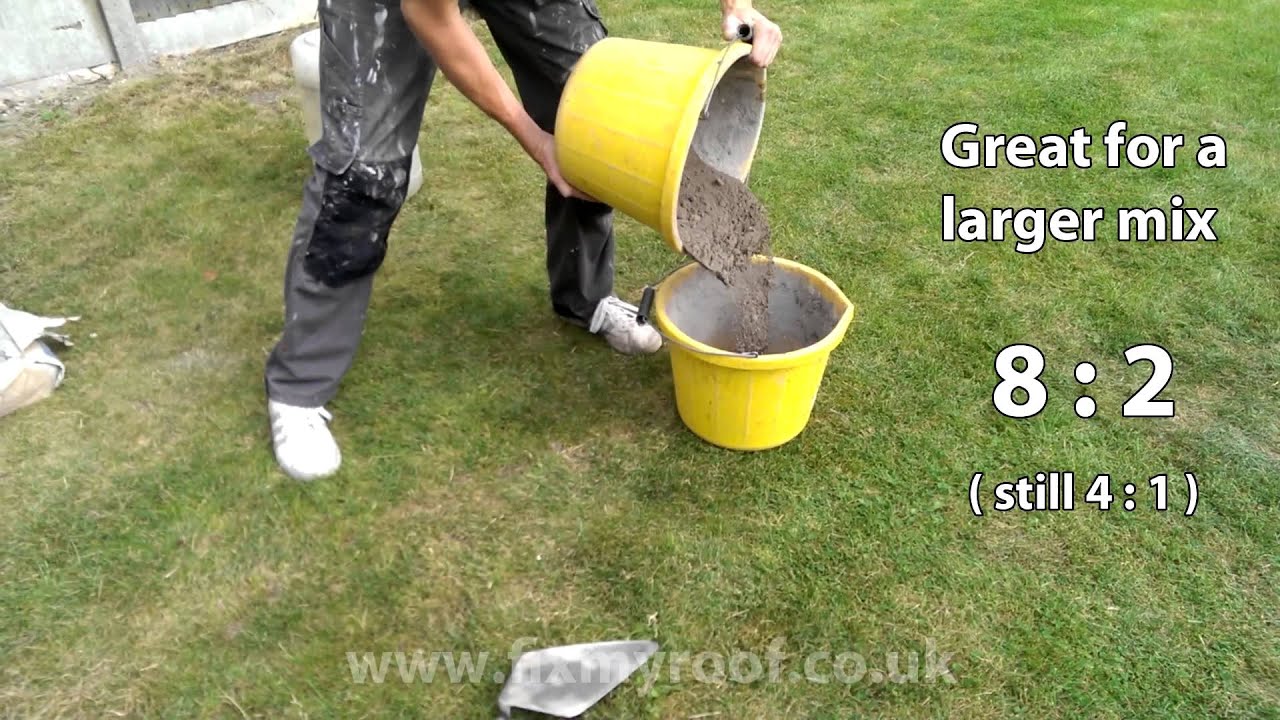
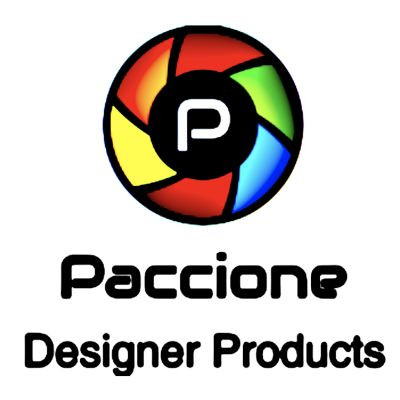
All opinions or methods expressed in the video(s) are personal opinion only and for educational purposes only. Always check current regulations or seek second opinions from other video sources or websites. Anyone working at ANY height should be fully trained and insured to do so and use the correct access equipment. Anyone working on ANY project does so at their own risk!
Mixing a small sand and cement bucket mix like this by hand is not only fast, but very cheap for small DIY jobs around the house. A lot of repair jobs even for professionals involve 'knocking up' small amounts of mortar like this. This is I believe an essential life skill, like knowing how to wire a plug, or unblock a sink.
Great for small pointing jobs, pointing lead flashings, brickwork chases, walls and chimney to name but a few...
For lager jobs why not consider a builders spot mix : http://youtu.be/ehBKETtRImk
For more help with common sand and cement mixes : http://www.fixmyroof.co.uk/mix-cement-mortar/
To learn how to point up a wall, slabs or chimney se this video : https://youtu.be/jPcp0iLoJtM
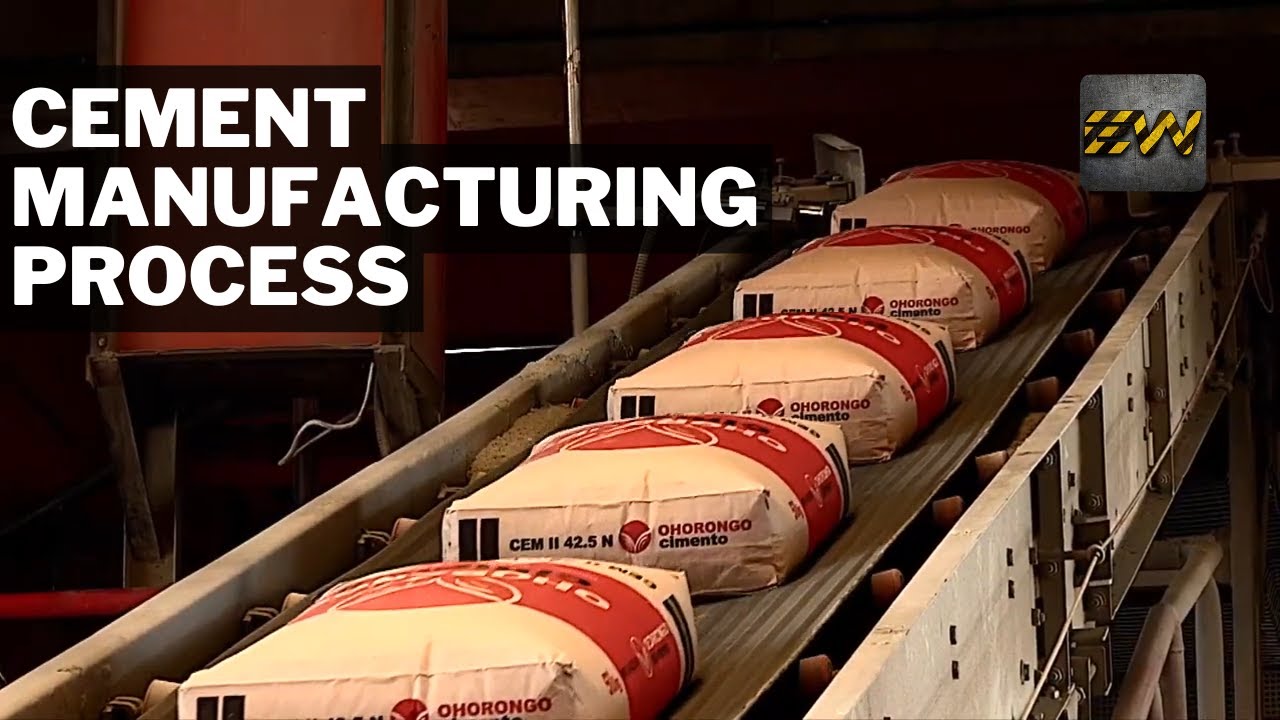
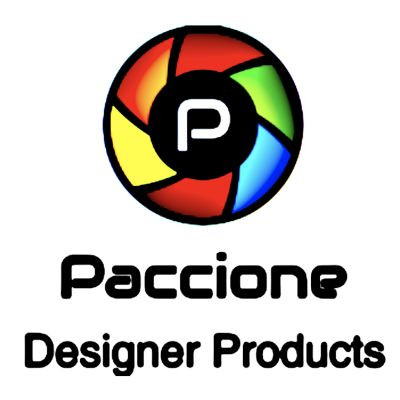
A cement is a binder, a substance used for construction that sets, hardens, and adheres to other materials to bind them together. Cement is seldom used on its own, but rather to bind sand and gravel (aggregate) together. Cement mixed with fine aggregate produces mortar for masonry, or with sand and gravel, produces concrete. Concrete is the most widely used material in existence and is behind only water as the planet's most-consumed resource.
Cement manufacturing is a complex process that begins with mining and then grinding raw materials that include limestone and clay, to a fine powder, called raw meal, which is then heated to a sintering temperature as high as 1450 °C in a cement kiln. In this process, the chemical bonds of the raw materials are broken down and then they are recombined into new compounds. The result is called clinker, which are rounded nodules between 1mm and 25mm across. The clinker is ground to a fine powder in a cement mill and mixed with gypsum to create cement. The powdered cement is then mixed with water and aggregates to form concrete that is used in construction.
Clinker quality depends on raw material composition, which has to be closely monitored to ensure the quality of the cement. Excess free lime, for example, results in undesirable effects such as volume expansion, increased setting time or reduced strength. Several laboratory and online systems can be employed to ensure process control in each step of the cement manufacturing process, including clinker formation.
Video Credits: www.ohorongo-cement.com
Join 'Engineering World' like many others to get access to special perks:
https://www.youtube.com/channe....l/UCh2wZoBynUkHmTX2G
Also, kindly consider subscribing to our channel if you liked the video: https://geni.us/SubscribeChannel
Watch some of our other interesting manufacturing videos:
How Plywood Is Made In Factories?
https://youtu.be/3Wh9NYvfStk
How LUXURY Rolls-Royce Cars Are Made ?
https://youtu.be/BVvnSzMqI3M
How Jigsaw Puzzles Are Made?
https://youtu.be/nylElsB9MkE

This video tutorial details the process of making a Poly 75-70 polyurethane rubber mold of a concrete stepping stone. In this example, we utilize the "poured block mold technique", which is considered to be one of the most simple mold making methods.
Although the stepping stones in this scenario can be easily replaced through options at retail stores, this mold making method is great when you have a unique stone that is not replaceable OR when you'd like to produce custom pavers from your original design (made from wood, clay, a printed model, etc.).
A full list of materials and tools used for this project can be found at the end of the video.
The Steps:
1. Select a Model [0:32]
2. Apply a Sealing Agent (Poly PVA Solution) [0:53]
3. Prepare Model and Construct Mold Box [1:24]
4. Apply Release Agent [3:33]
5. Calculate Amount of Rubber Needed for Mold [4:13]
6. Measure, Mix & Pour Mold Rubber [5:03]
7. Demold [6:29]
8. Cast Concrete [7:24]
http://www.polytek.com
http://www.facebook.com/polytekdevelopmentcorp
http://www.twitter.com/PolytekUSA
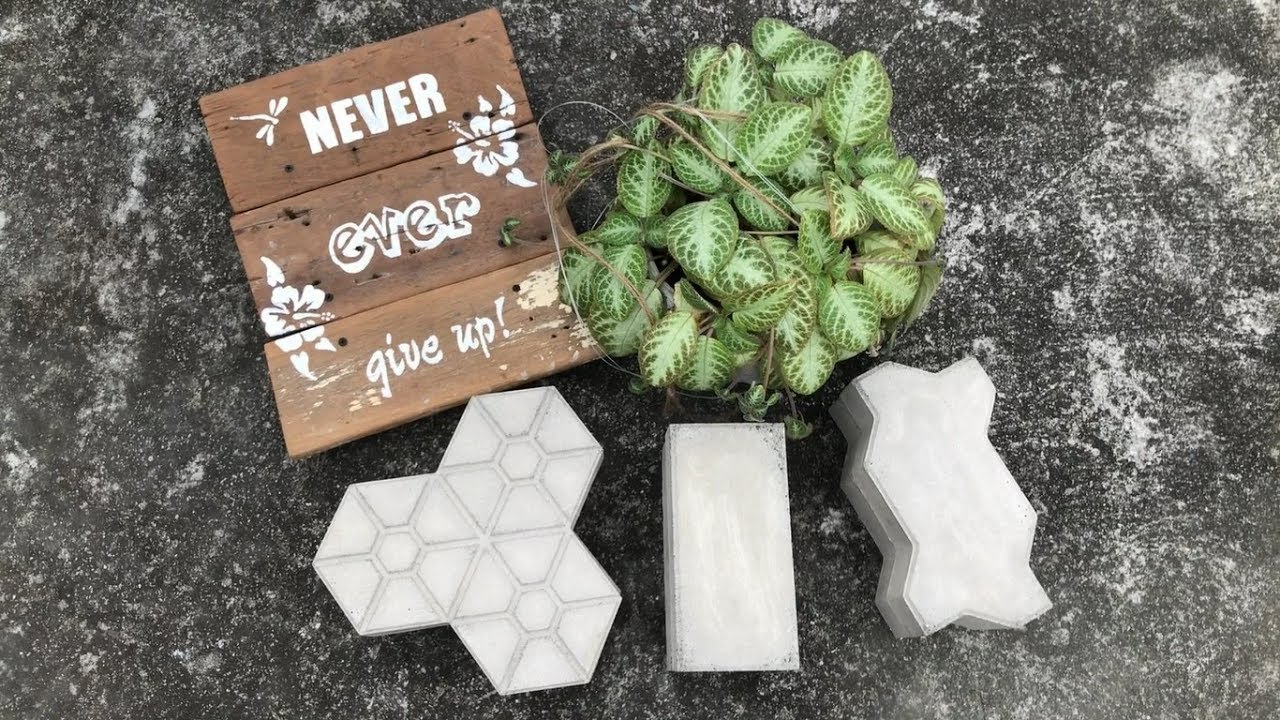
You can use concrete paver blocks as edging for your garden beds, or to give your driveway a makeover.
In this video, I'd like to share how I make concrete paver blocks using plastic molds. Also included are tips on how to demold properly so that you can minimize your chances of damaging the resulting blocks.
The plastic molds I used come in different shapes. In the video, you'll find 3 options. Get these paver molds here: http://s.click.aliexpress.com/e/rqYgPVRi
#HowtoMakeConcretePavers
#HowtoUseConcretePaverMolds
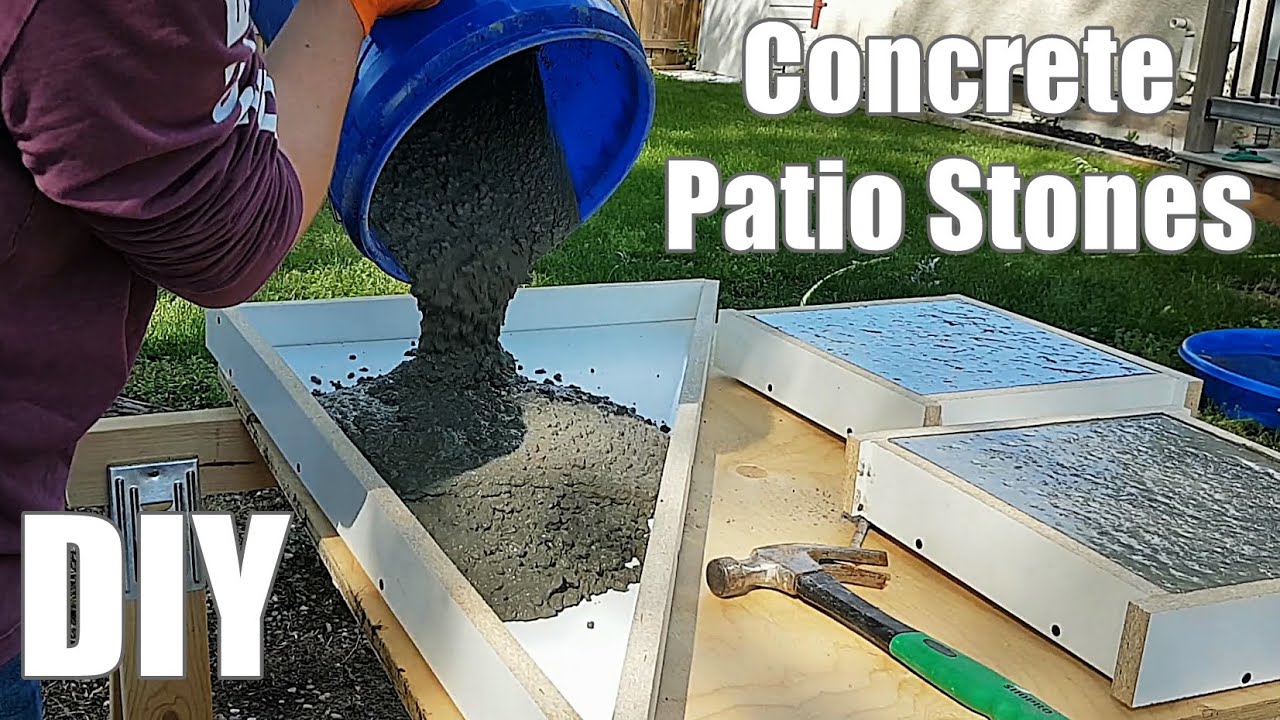
This is a great beginner project for dipping your toes into concrete projects! I go over the steps to create basic concrete shapes and forms, and pouring. No crazy steps or perfection needed since it's just a block, so have fun and practice!
I know they are inexpensive to buy, but around here they go out of season, or you may need a shape or size they don't sell, so this can come in handy for different situations.
Help support the channel and the things I can show by using the links below, it costs nothing to use them, but helps me out so I can help you!
Get the Freshest CA Super glues in the market at Starbond (https://bit.ly/2KPcQTa)
Use Code CANADIYAN at checkout to save 15% off on your purchase!
**************************************
Jesse Does DIY links:
🛠Email: jessedoesdiy@gmail.com
🛠Project Plans: https://jessedoesdiy.etsy.com
🛠Instagram: https://www.instagram.com/canadiyan_jesse/?hl=en
🛠Instructables: https://www.instructables.com/....member/Jesse+does+DI
Other Channel with Slade:
https://www.youtube.com/channe....l/UC-qQtqcjoWHbNn9Kg
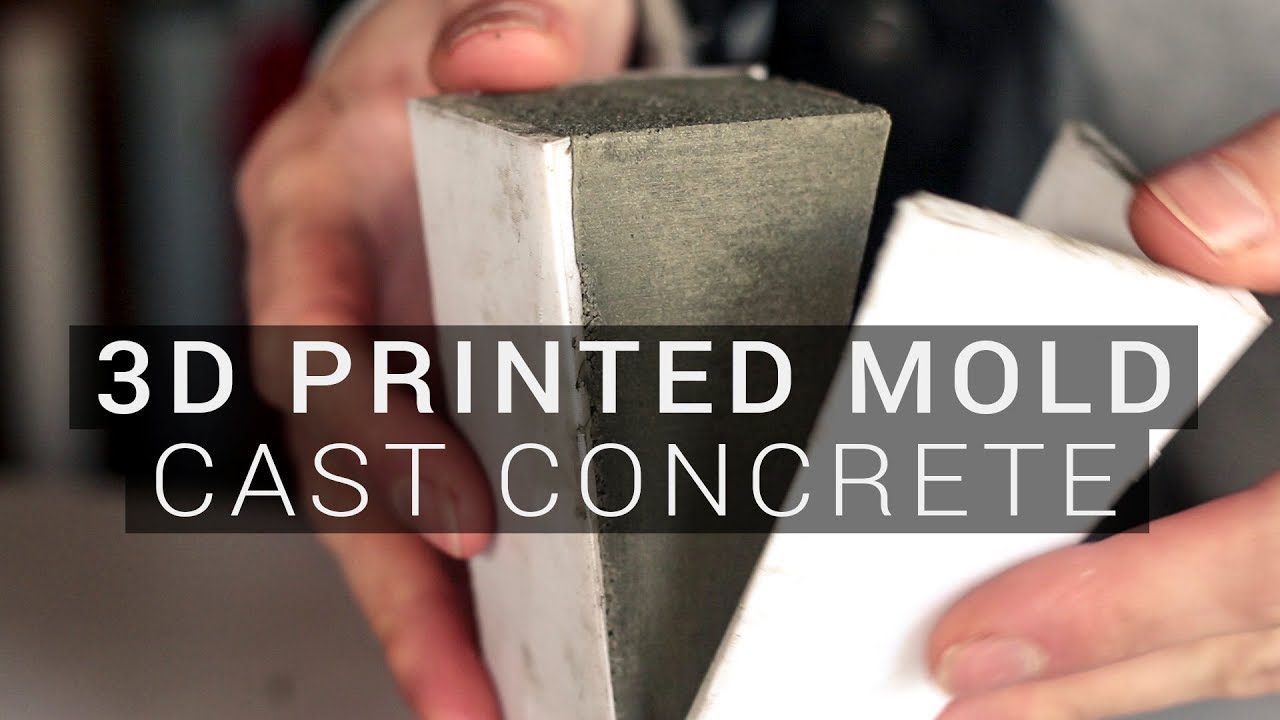
How to use 3d printed molds to create cast concrete products and objects - without needing any silicone.
All Project files are available free from my website:
https://www.furtherfabrication.com/resources
Find me on instagram:
https://www.instagram.com/further_fabrication/
Link to Fusion 360 software:
https://www.autodesk.com/produ....cts/fusion-360/stude
Music:
https://www.epidemicsound.com/